Our optimization service includes the five fields of plastic part production: part design, mold, runners' systems, materials and mold flow analysis. The mold flow support us in suggesting improvements. An anomality seen during the analysis that can be modified could enhance the complete process of the production. Can the cycle time be improved? This can go through a cooling analysis or, in other cases, finite element analysis (FEA). Do you need to optimize deformations? Do you need more information on the warp? Do you want optimize the production? Do you want to reduce the weight of the plastic parts? Solution M2 is here to help!
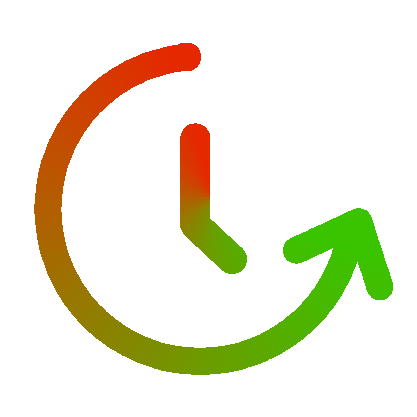
Production Optimisation
Simple solutions to possible problems can be found using the mold flow while it can be more complex to do so on the factory floor. The mold flow supports us in suggesting improvements. An anomaly seen during the analysis that can be modified could enhance the complete process of the production. The mold flow is more than a prediction tool, it serves as a communication tool between the different authorities within the organization. Via visual support of the making of the plastic part, people involved in the production process will be able to use the simulation as a tool to ensure a good flow within the projects. In the best case, the analysis should be done at the start of mold production to begin adjustments before it is too late.
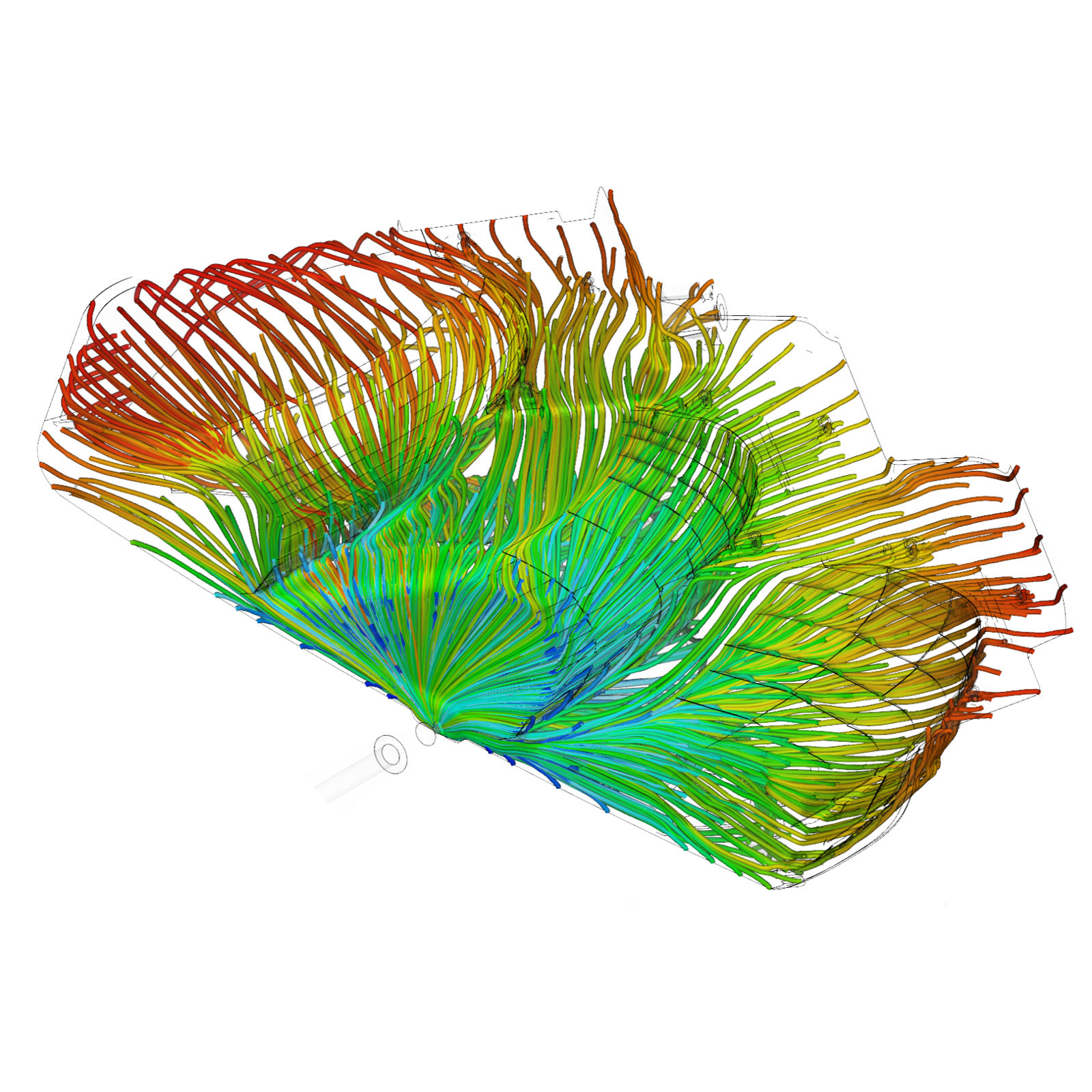
Plastic Flow
Phase 1
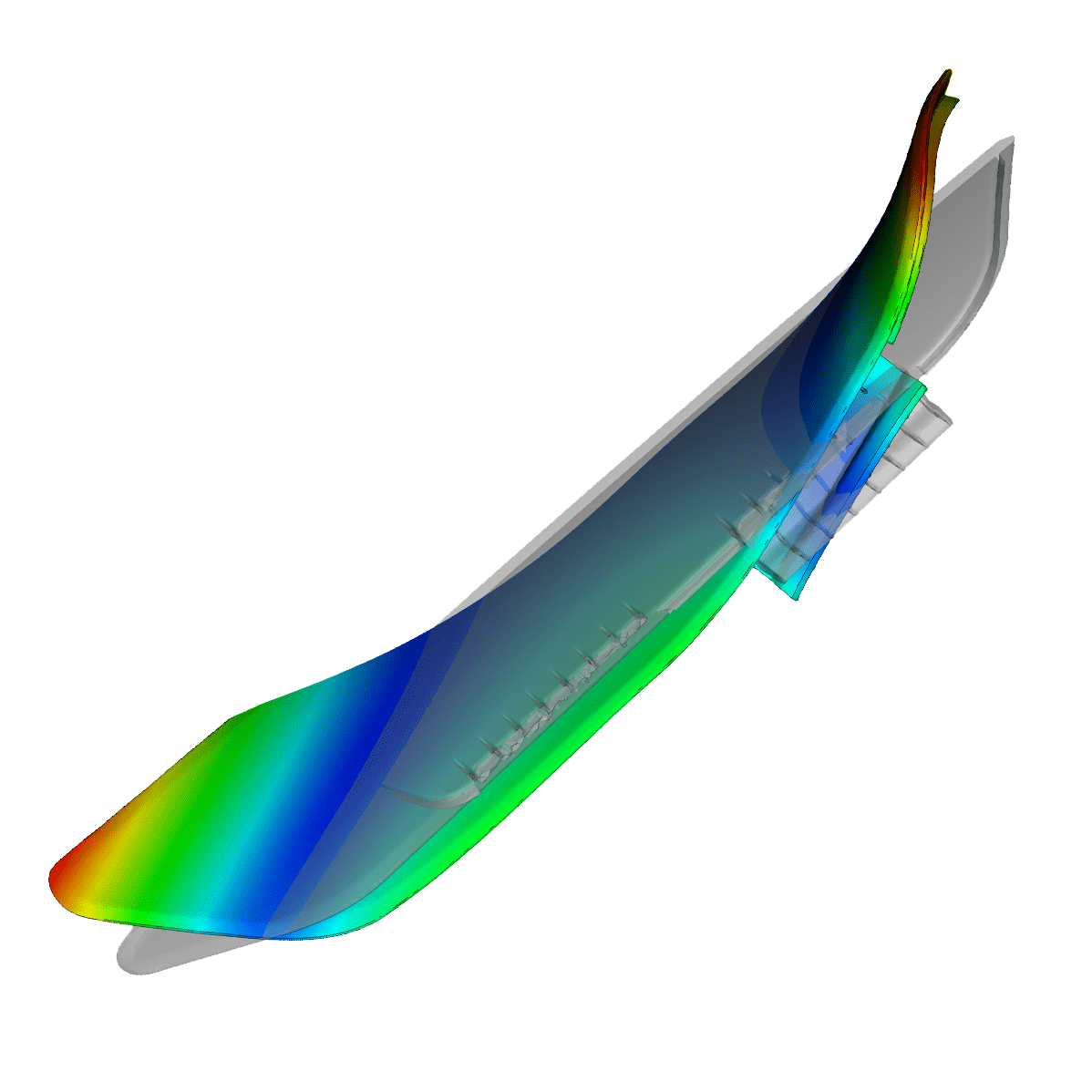
Part Warping
Phase 2
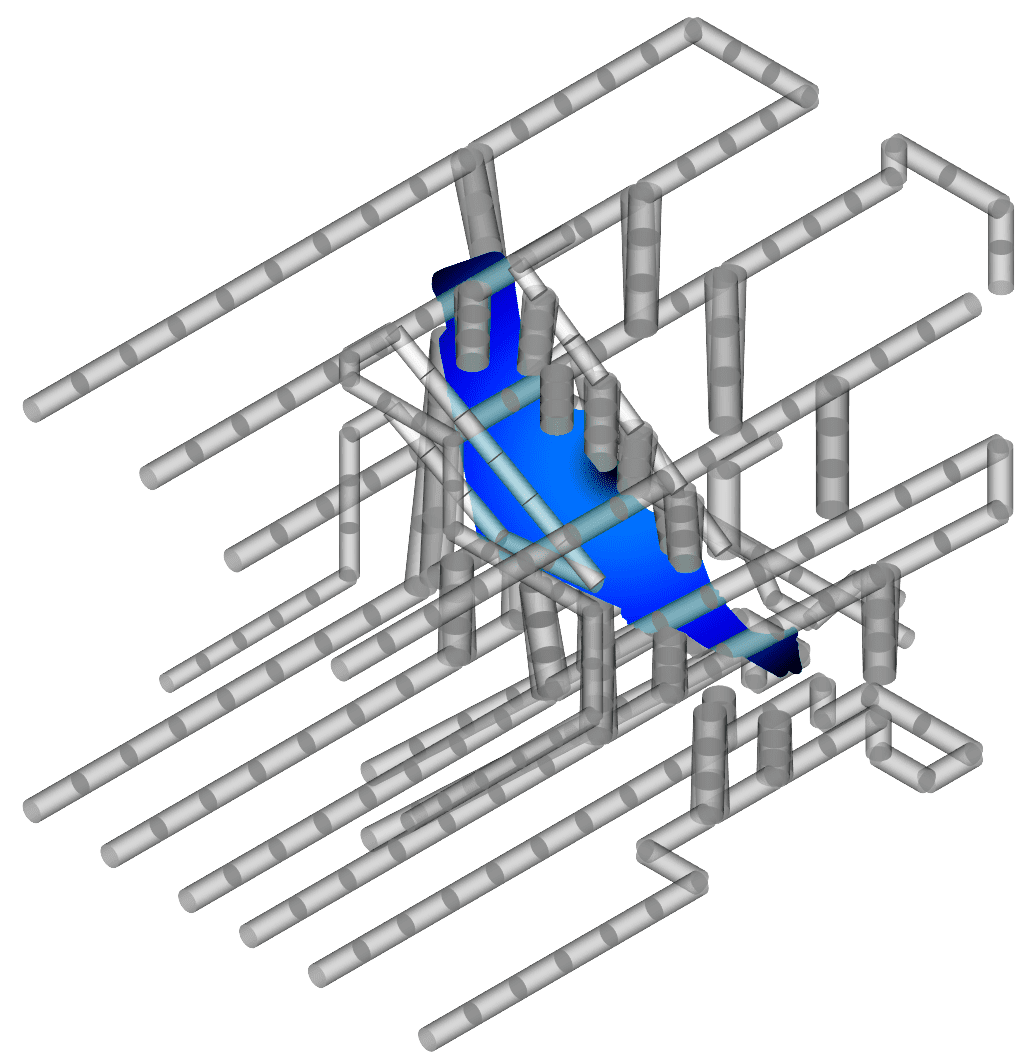
Mold Cooling
Phase 3
Cooling helps you get the best cycle time possible while using less energy. This could be complete tooling for the production of your plastic parts. Is the cooling optimal depending on the part? Do I have enough cooling lines? How cycle time can be improves with a MoldMAX insert?
Phase 3 is an optimization of the cycle time, but also an optimization of the part warping. You need to optimize the deformations and have more information on the warp? We will determine the right amount of cooling lines instead of drilling everywhere. This is a complete tool for the production of your part.
Optimize Deformation
Efficient Cooling
Reducing Cycle Time
Mold Performances