Air Trap
It is always important to balance the plastic supply of the part. Modifying the fuel system can change the fill pattern so that the areas that fill last are in places that allow adequate air evacuation. Most air traps that cause problems do not occur in areas that can easily be provided with air exhaust. The main air evacuator systems are the joint plan, insert or ejectors.
Here are some causes:
- The press closing force is too high ;
- Lack of rigidity in the mold structure ;
- Closing problem at the mold level.
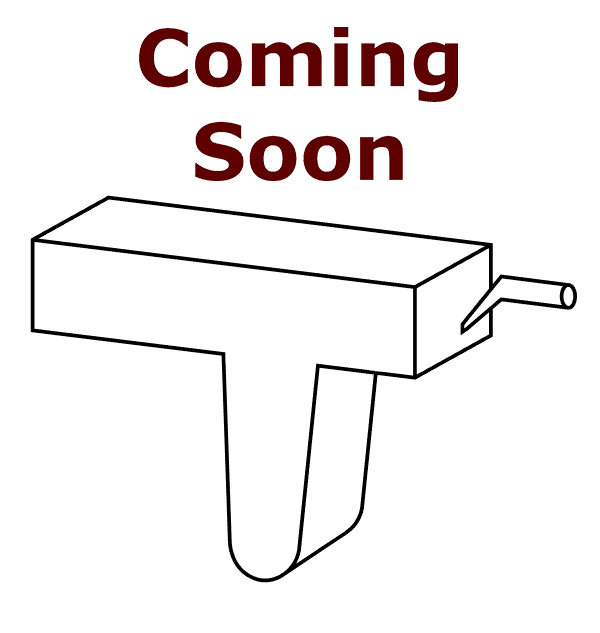
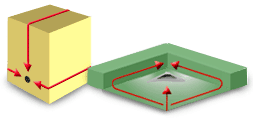
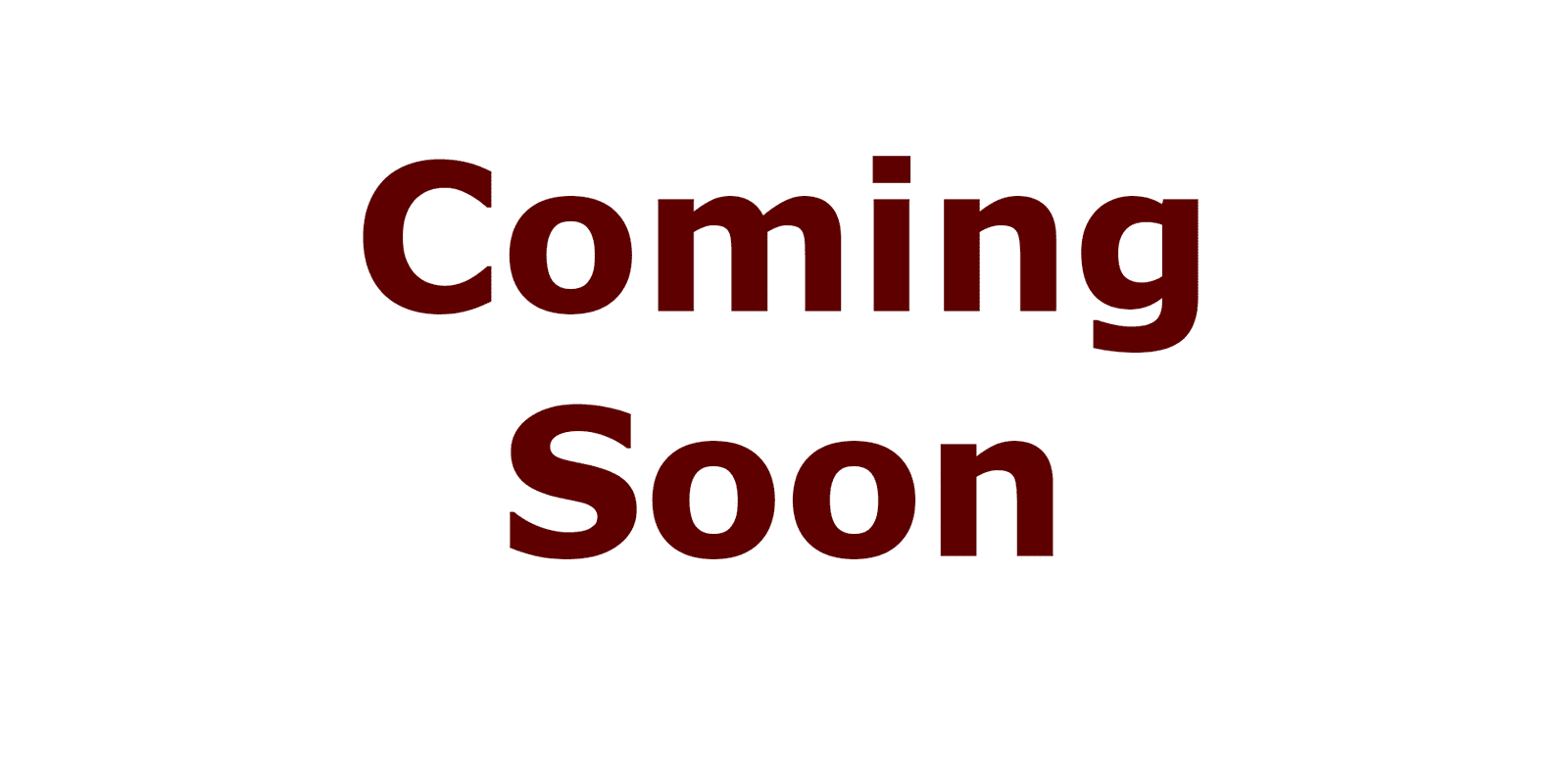
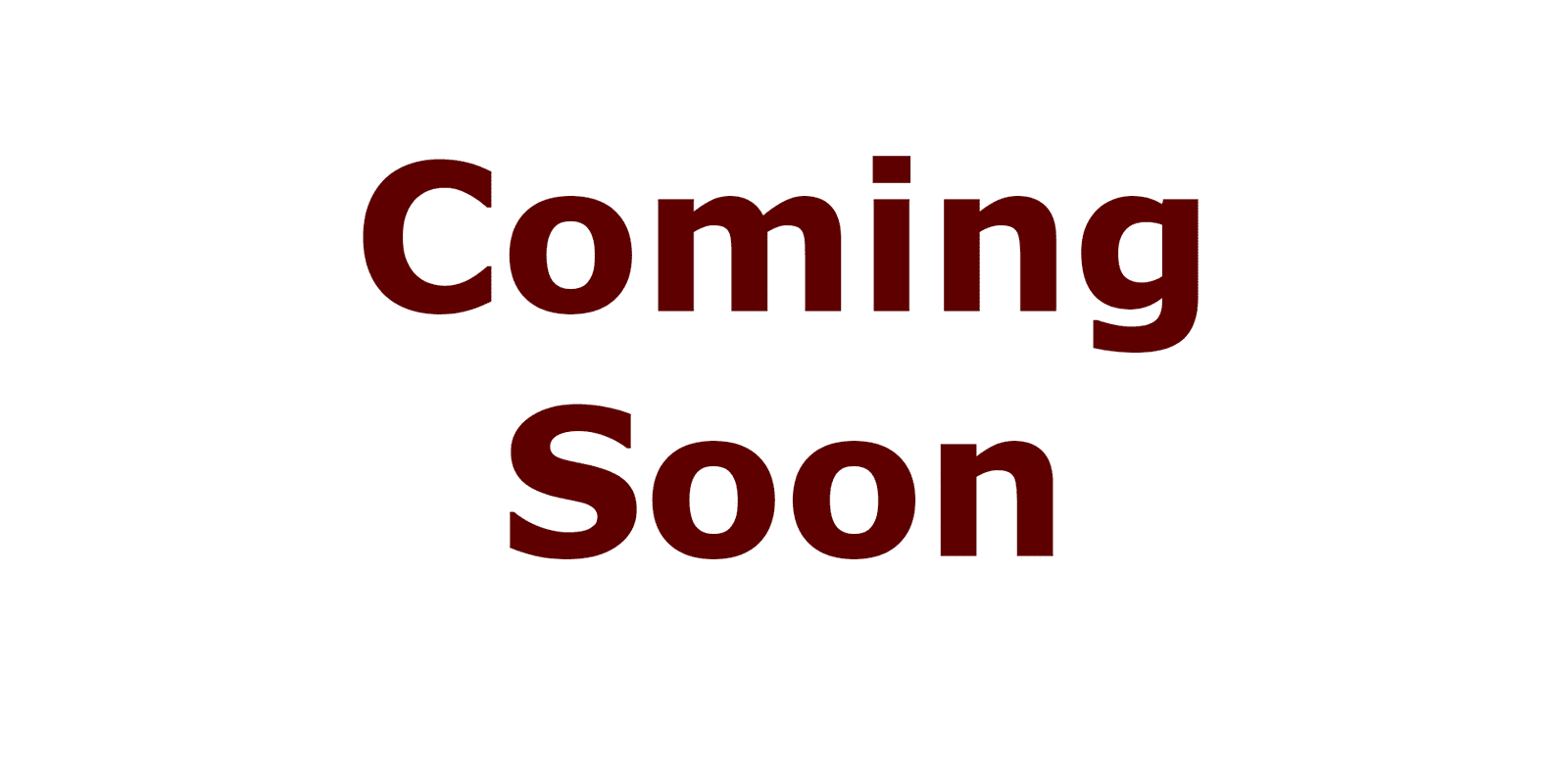
Burn
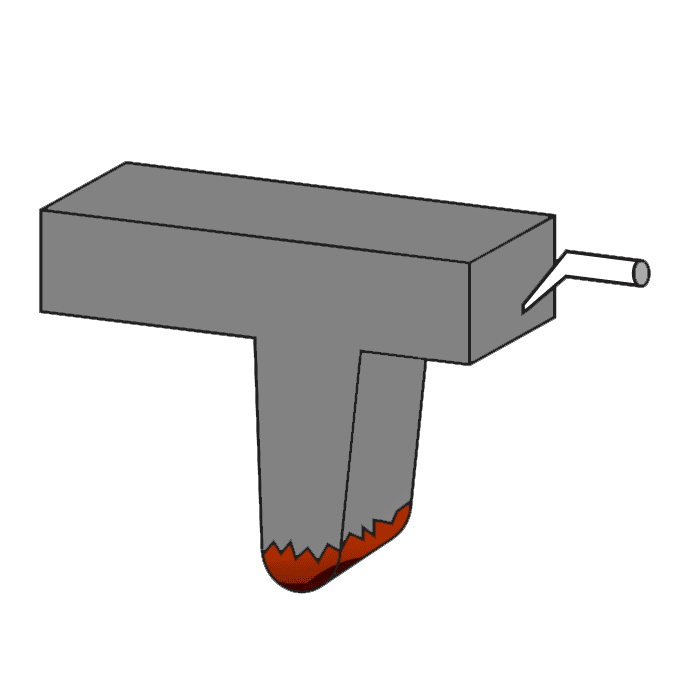
When the residence time of the material is exceeded, the plastic deteriorates. This happens when the plastic stays too long in liquid form, therefore heated. I Scorch marks are small dark or black dots on the surface of the part.
Here are some causes:
- Significant release of volatile compounds in the polymer ;
- Excessive decompression after dosing ;
- Inefficient vents (vents) system ;
- Long-heated polymer.
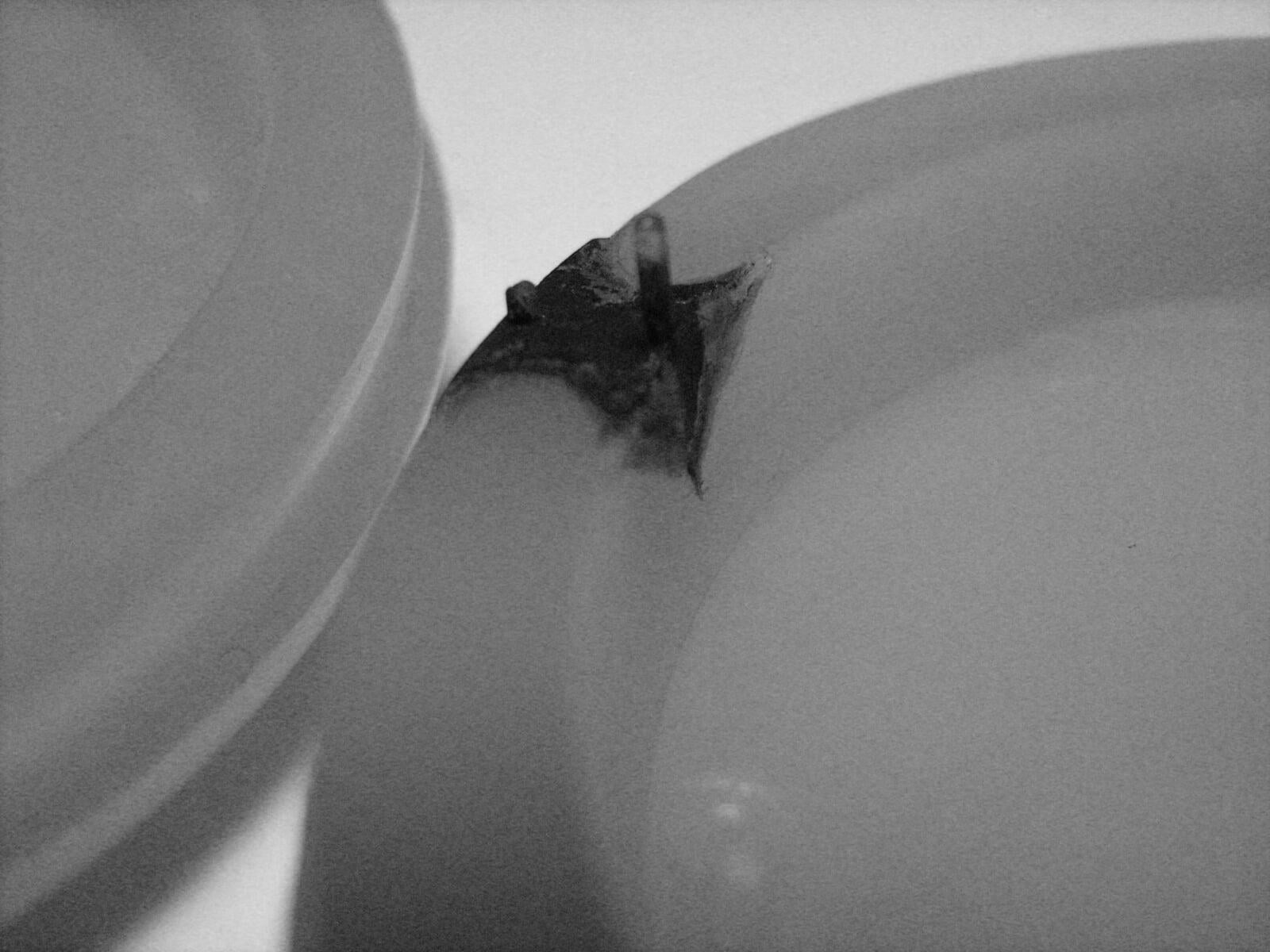
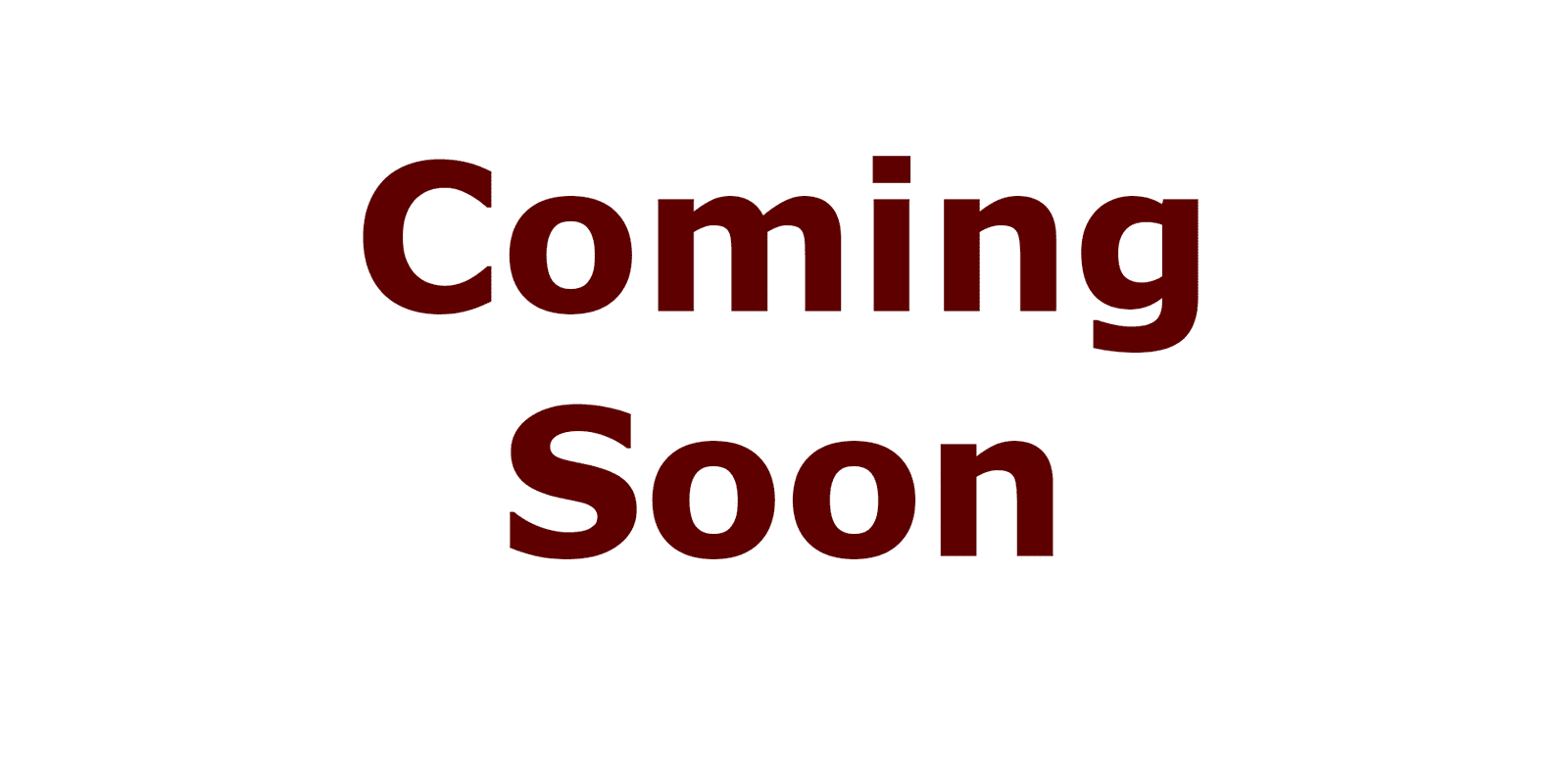
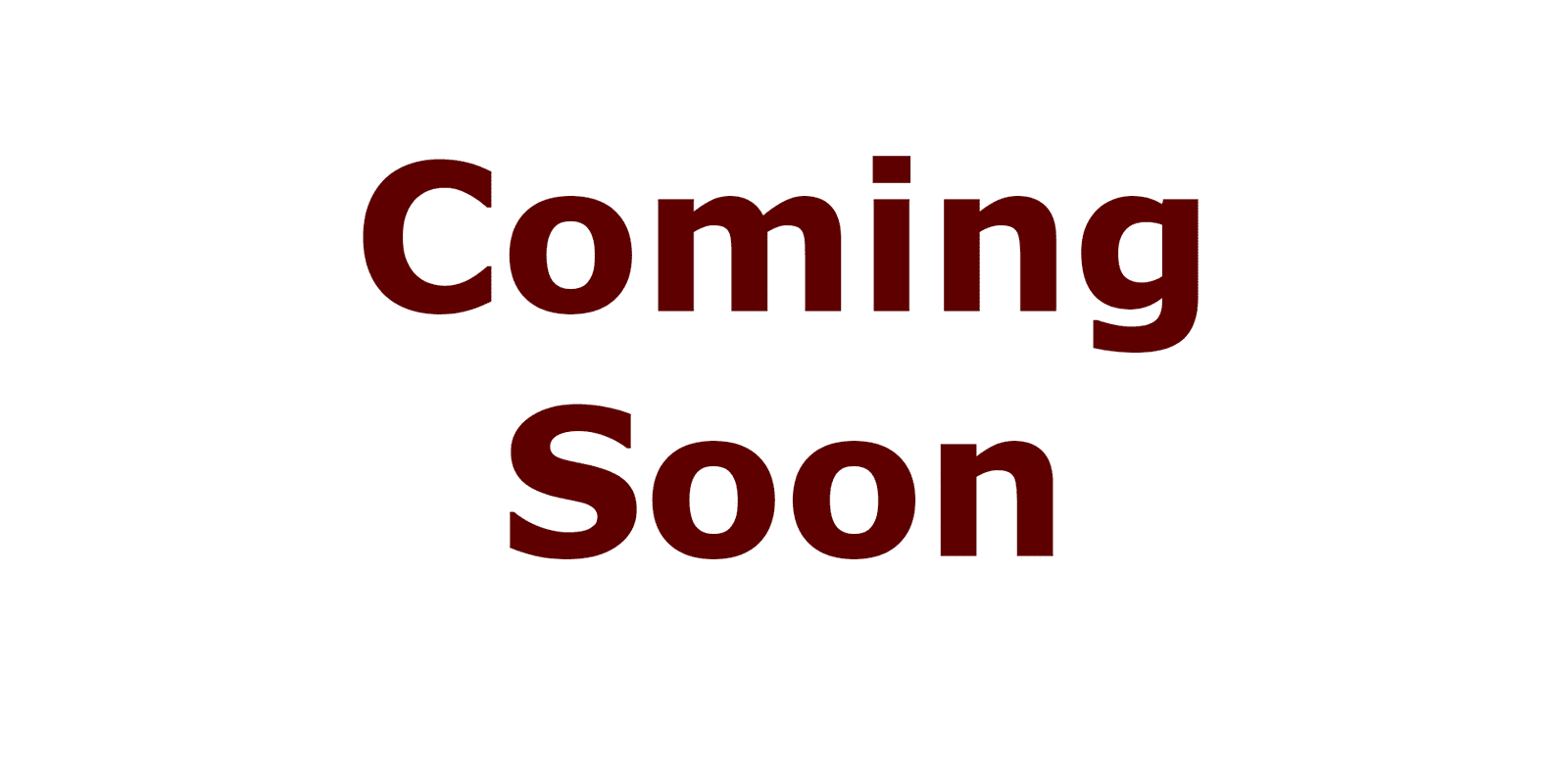
Cycles
COMING SOON
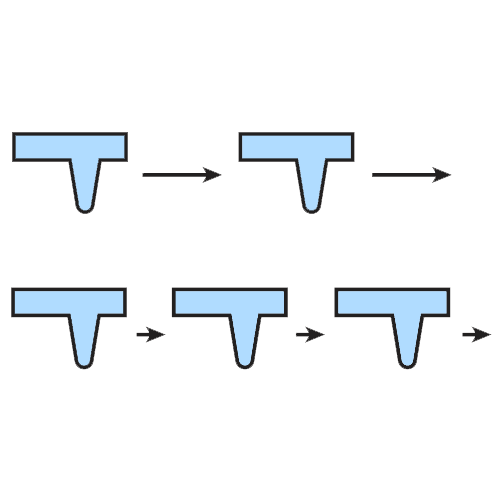
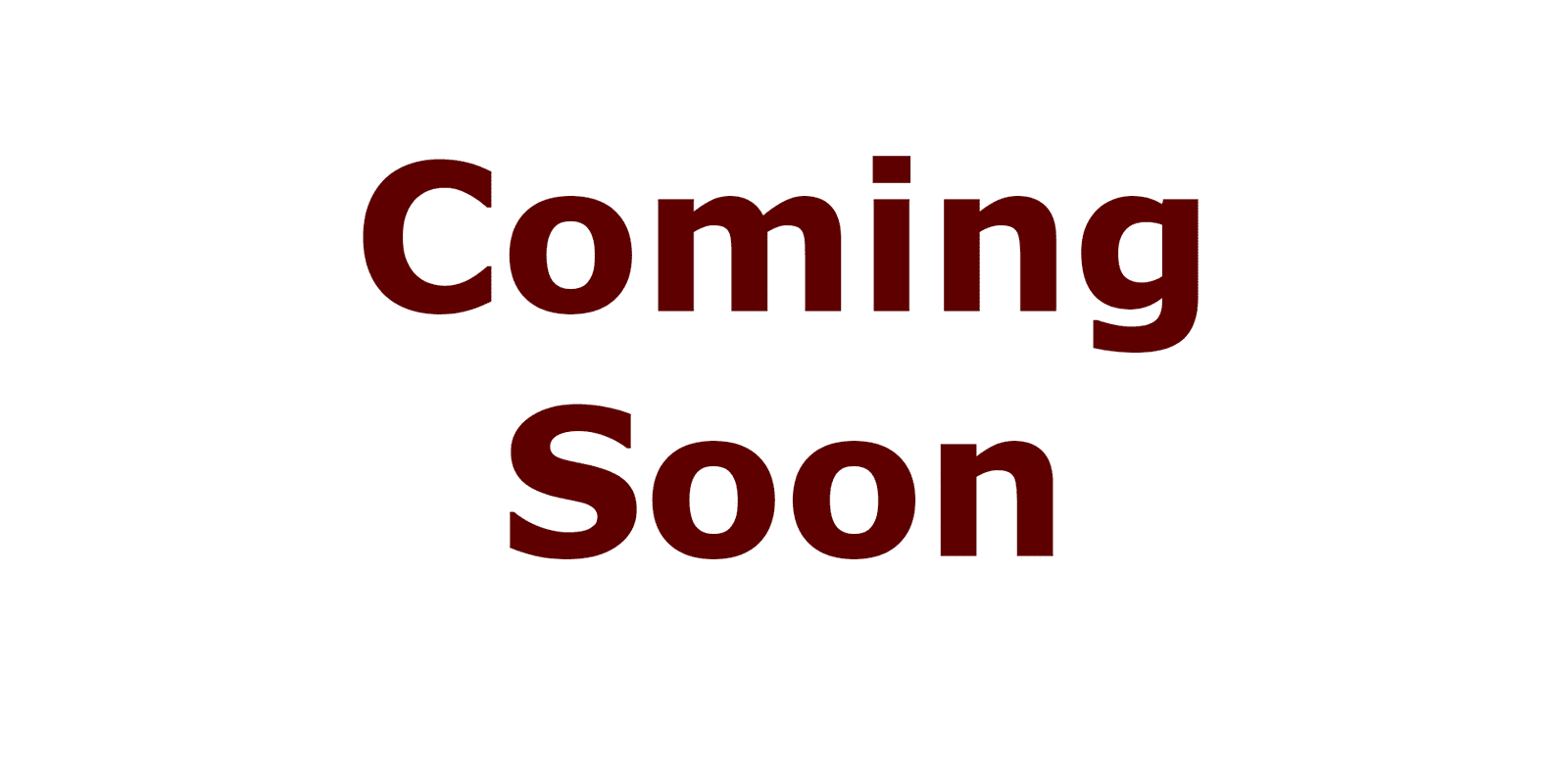
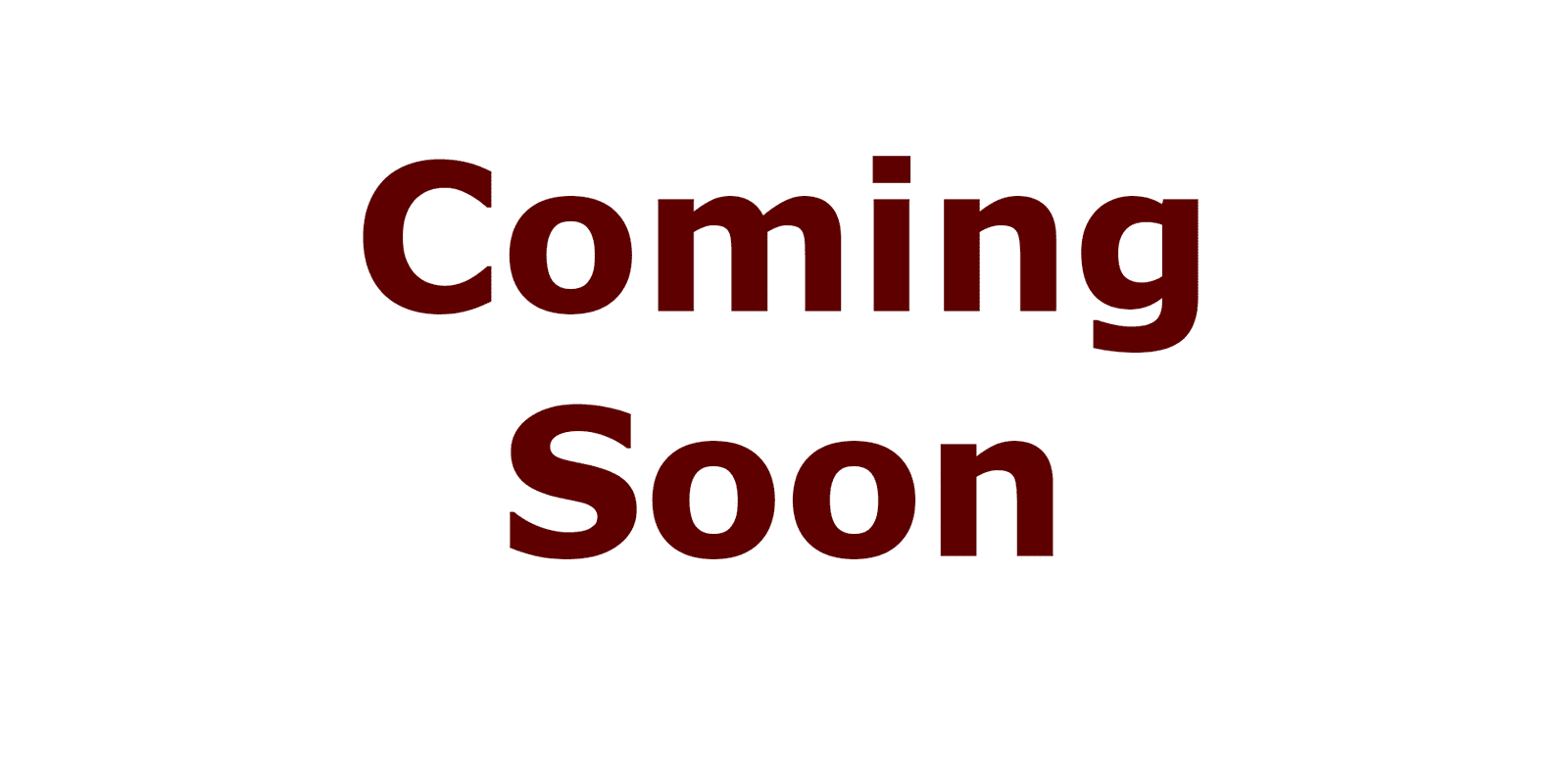
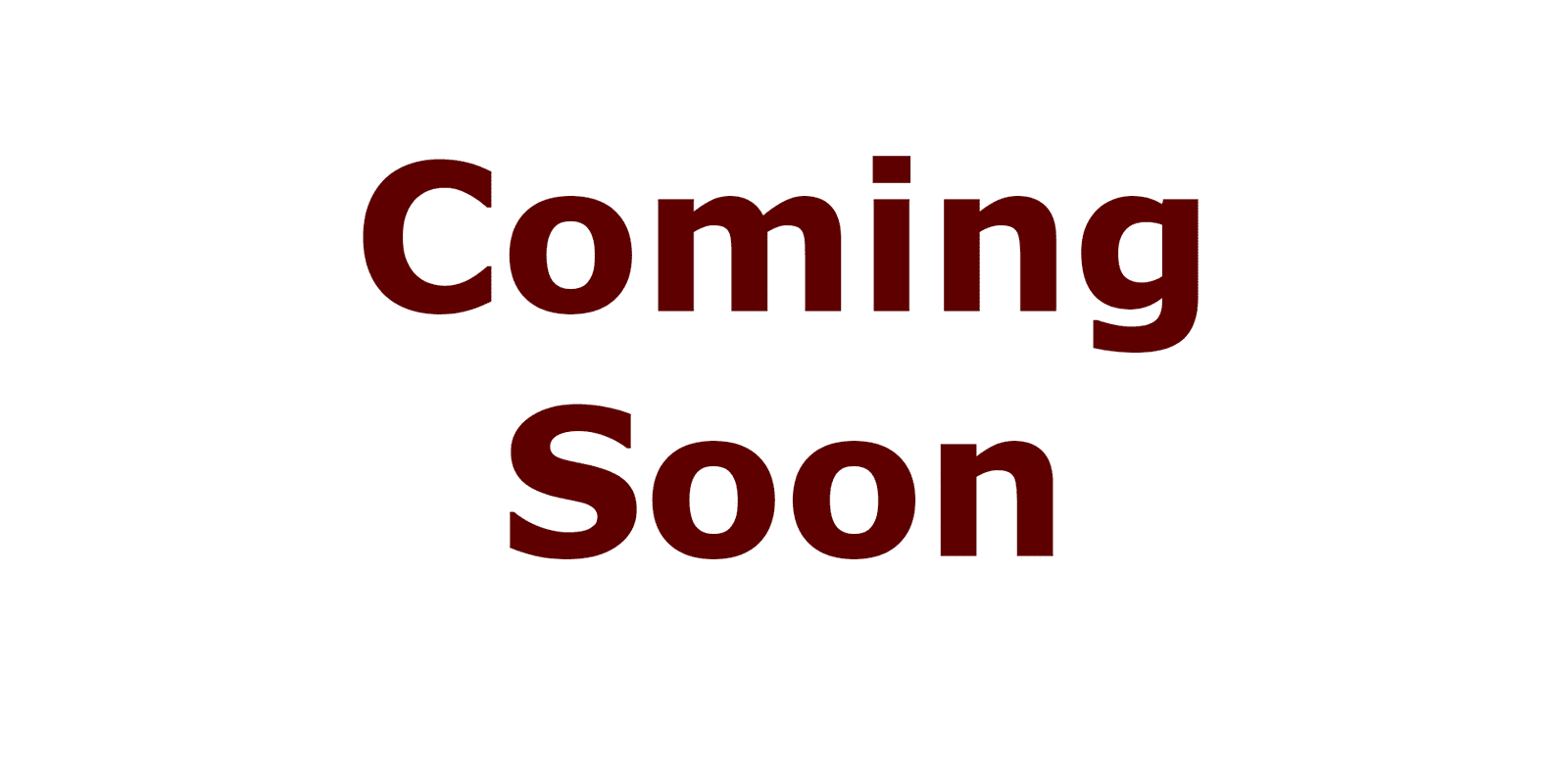
Flash
Flashing occurs when the material is pushed out of the mold cavity. The plastic comes out at the parting line or the ejector pins. This creates a sheet of plastic that is glued to the piece. Often it is said that it is the mold itself which flashes.
Here are some causes:
- The barrel temperature is too high ;
- The closing problem at the level of the mold dirt, misalignment at the level of the joint plane ;
- Compaction pressure (holding pressure) too high ;
- Press closing force is too low ;
- The switching point (V/P) occurs too late in the process.
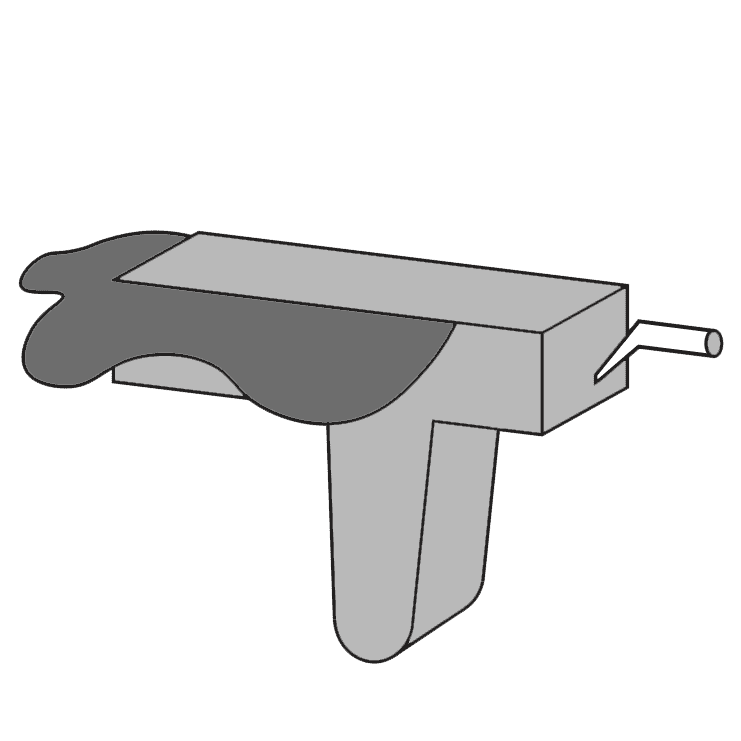
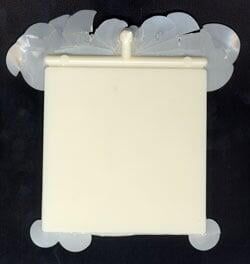
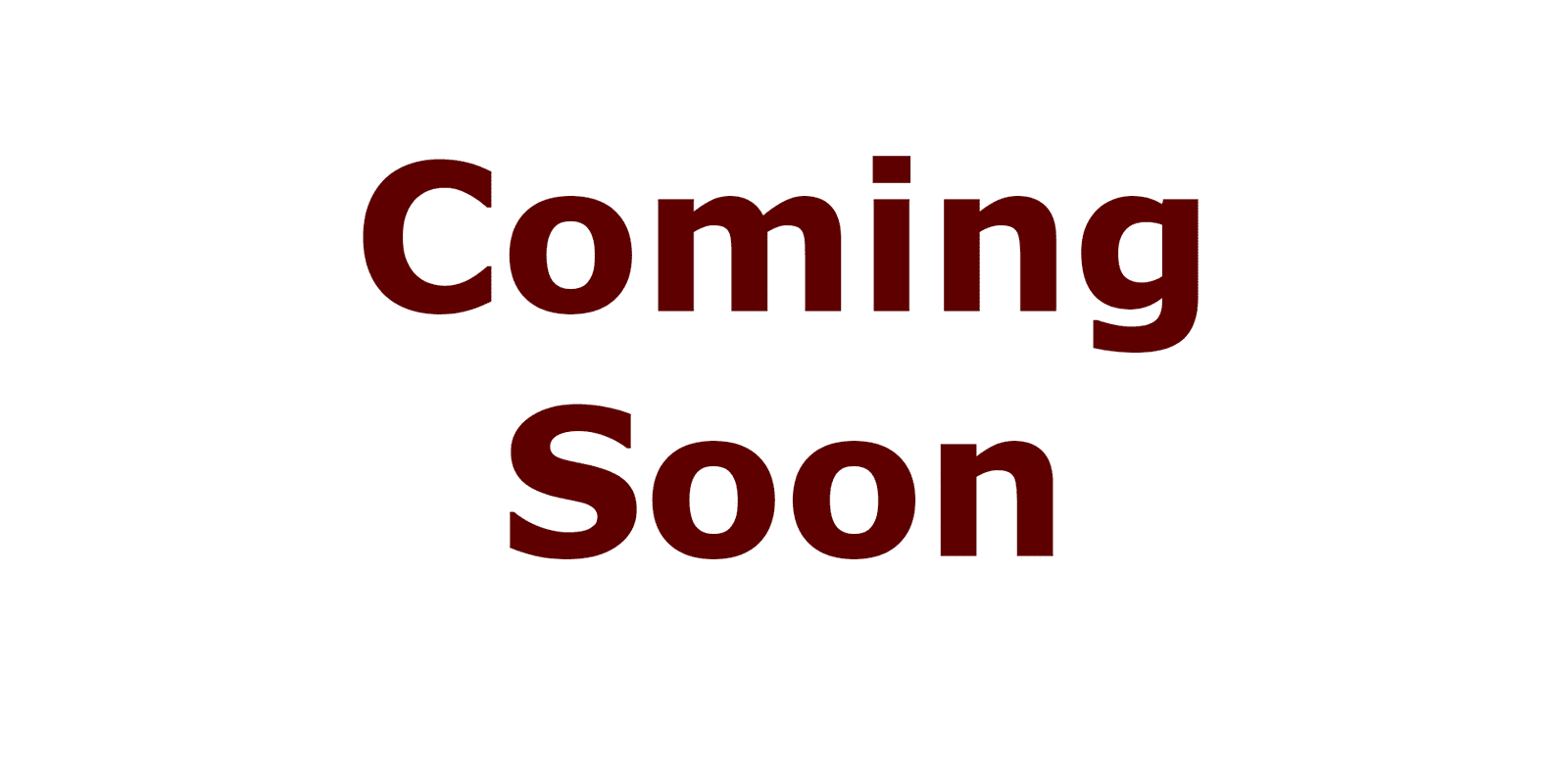
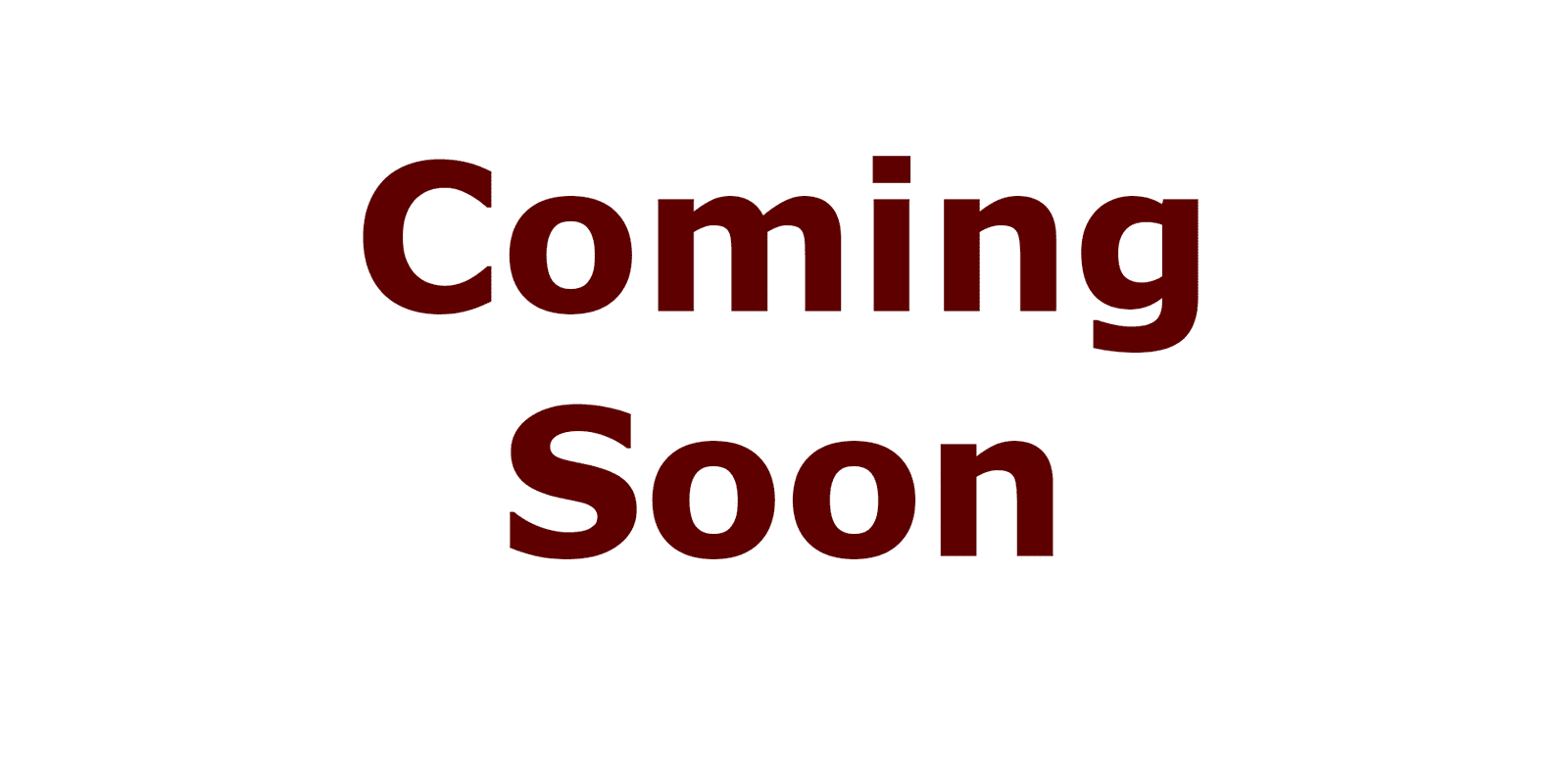
Jetting
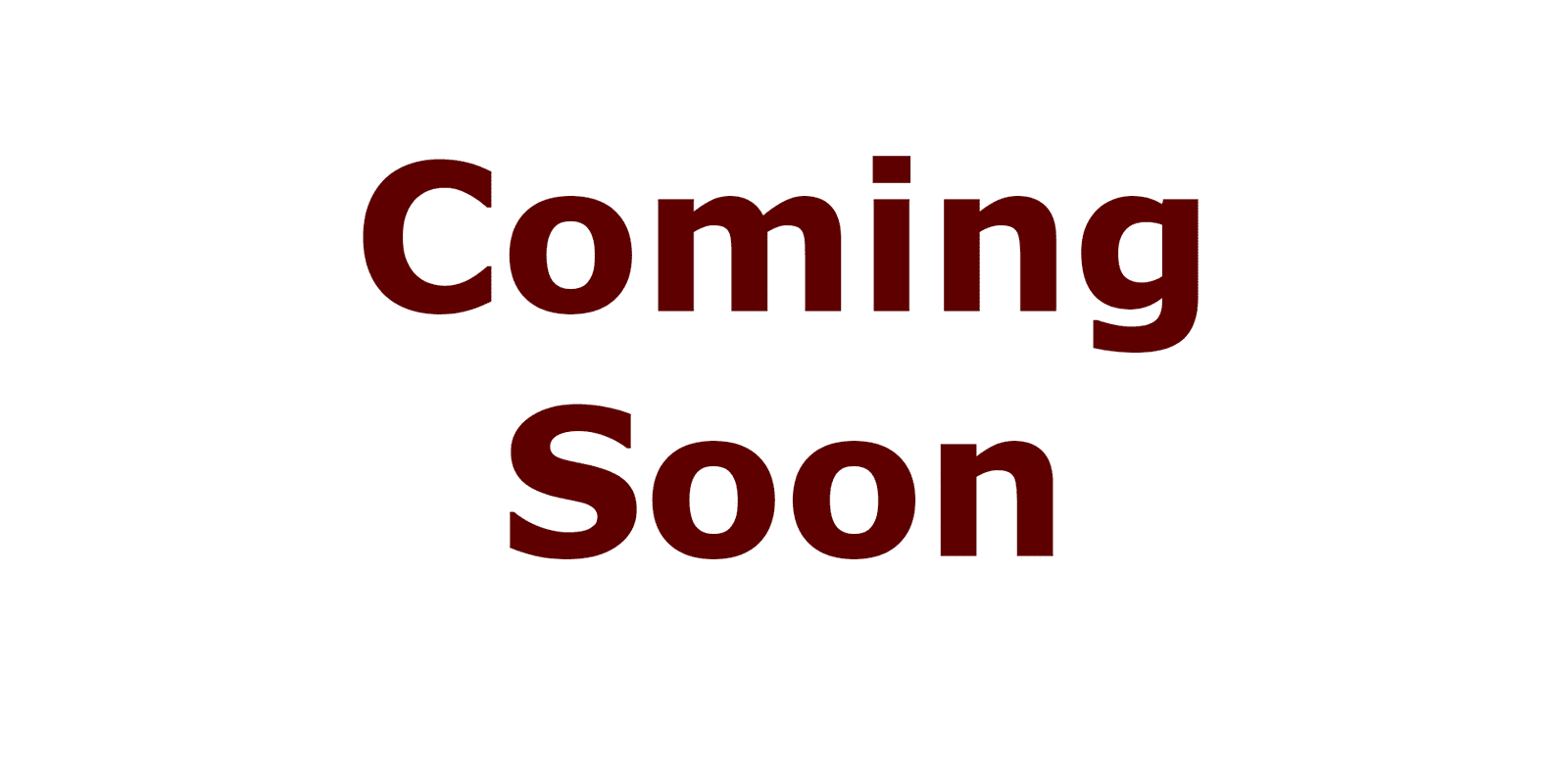
The free jet occurs when the material penetrates at too high a speed inside the mold. The size of the gate or the pressure is often in question. The free throw results in surface imperfections and several internal defects that affect the strength of the part.
Here are some causes:
- A bad design of the runner system ;
- Bad design gate ;
- An excessive piston speed.
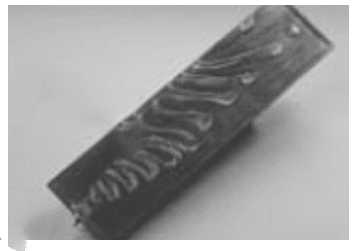
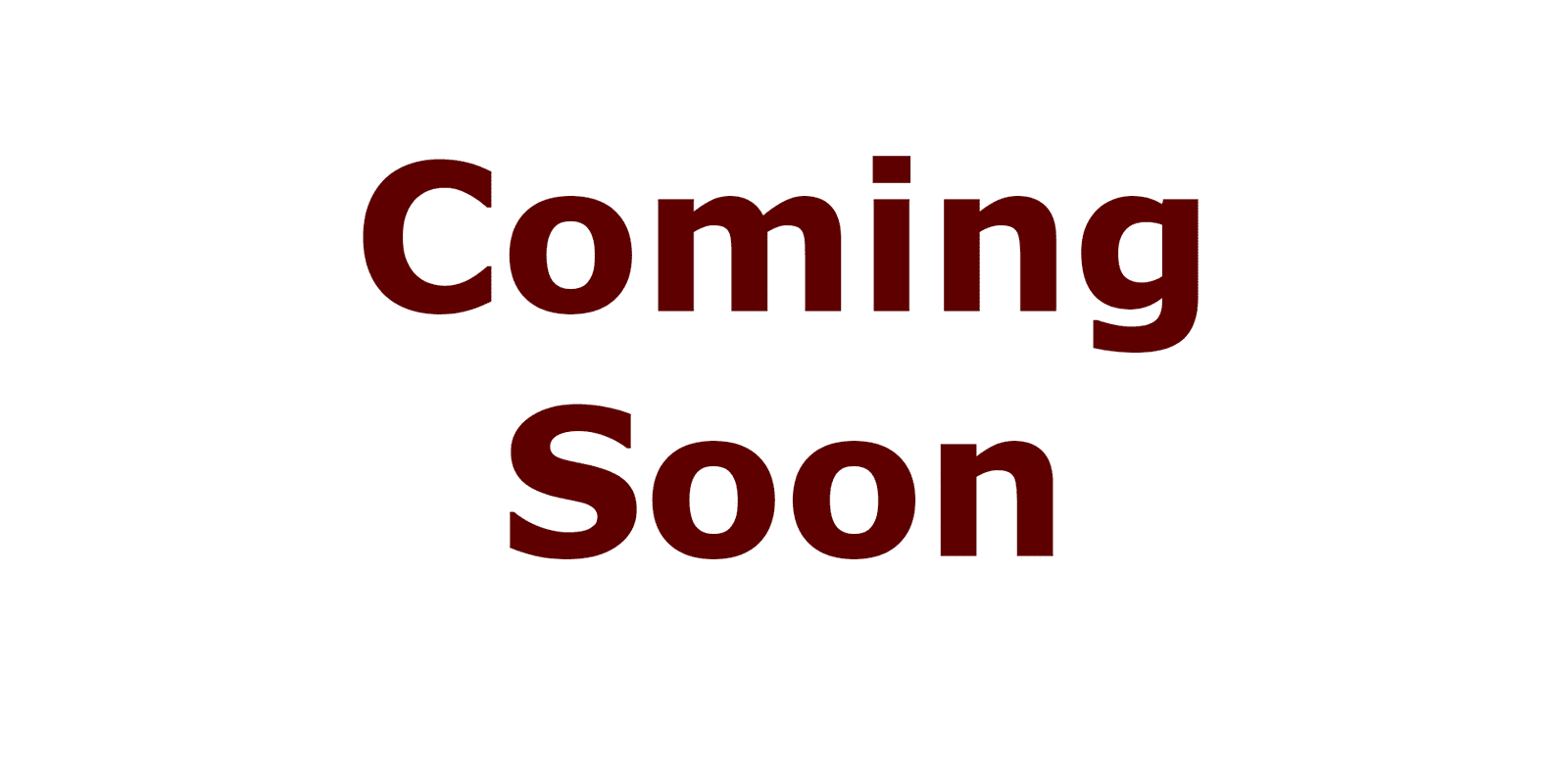
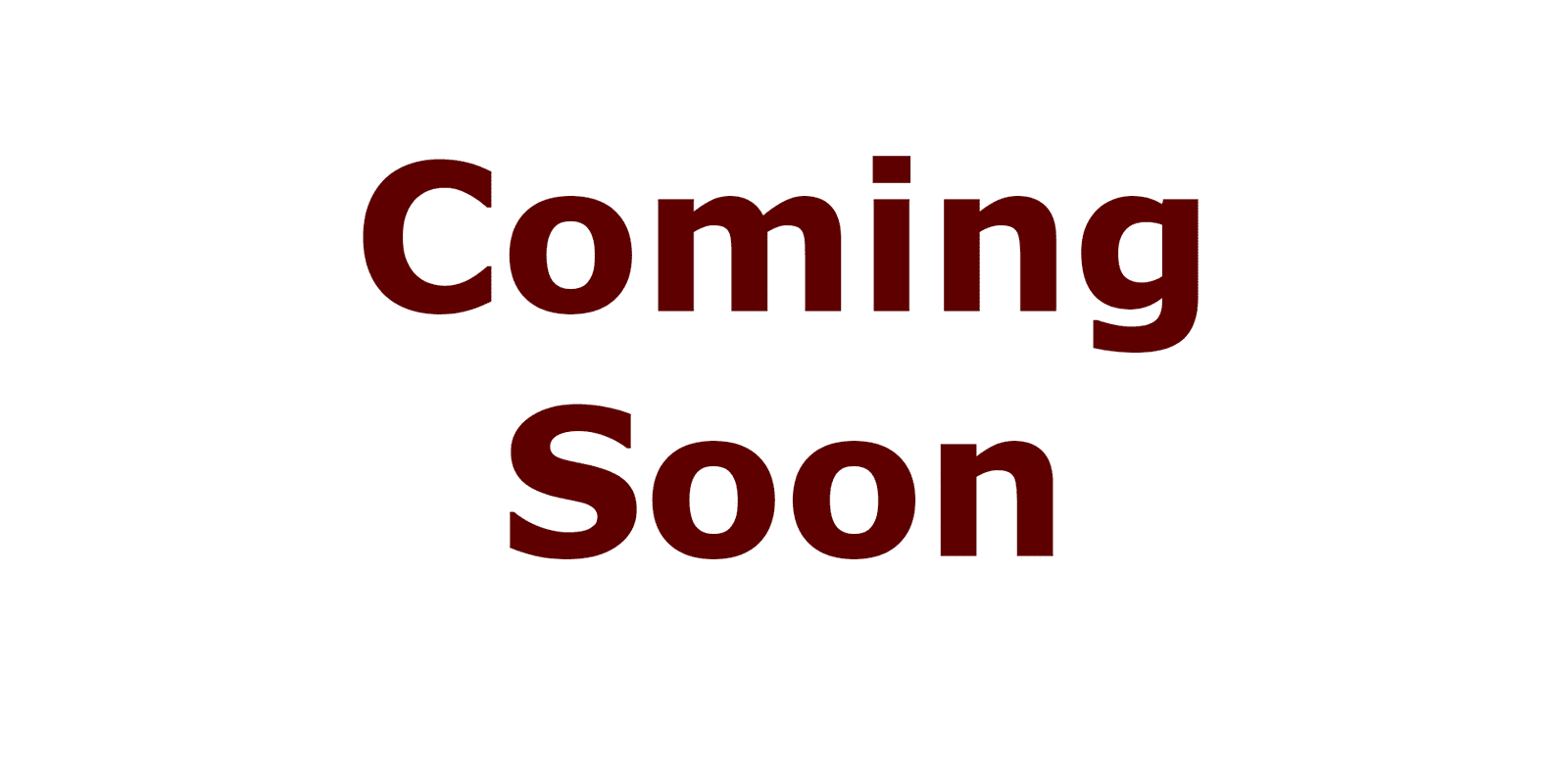
Production
COMING SOON
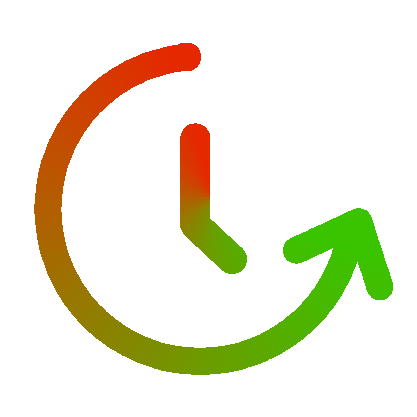
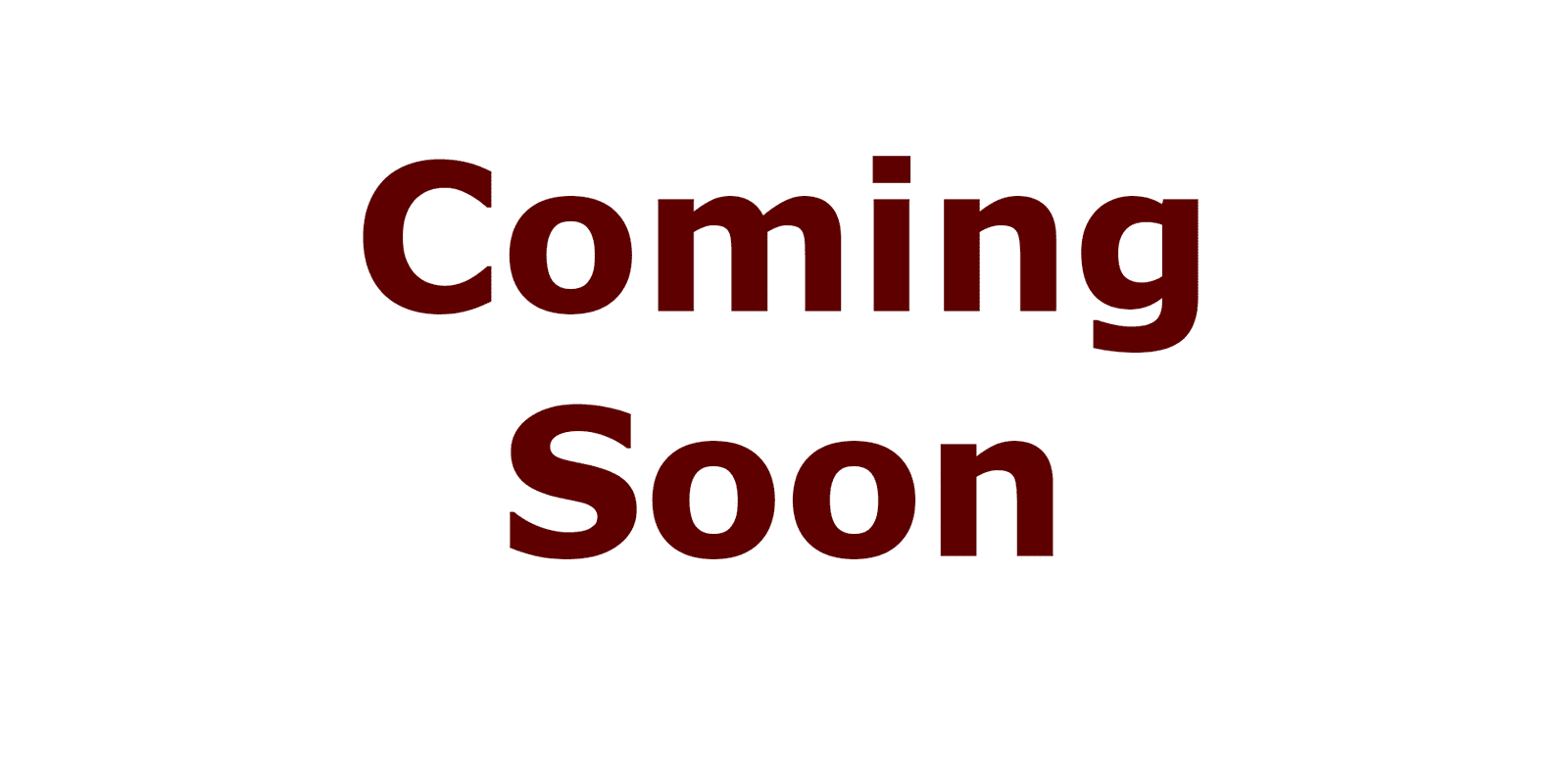
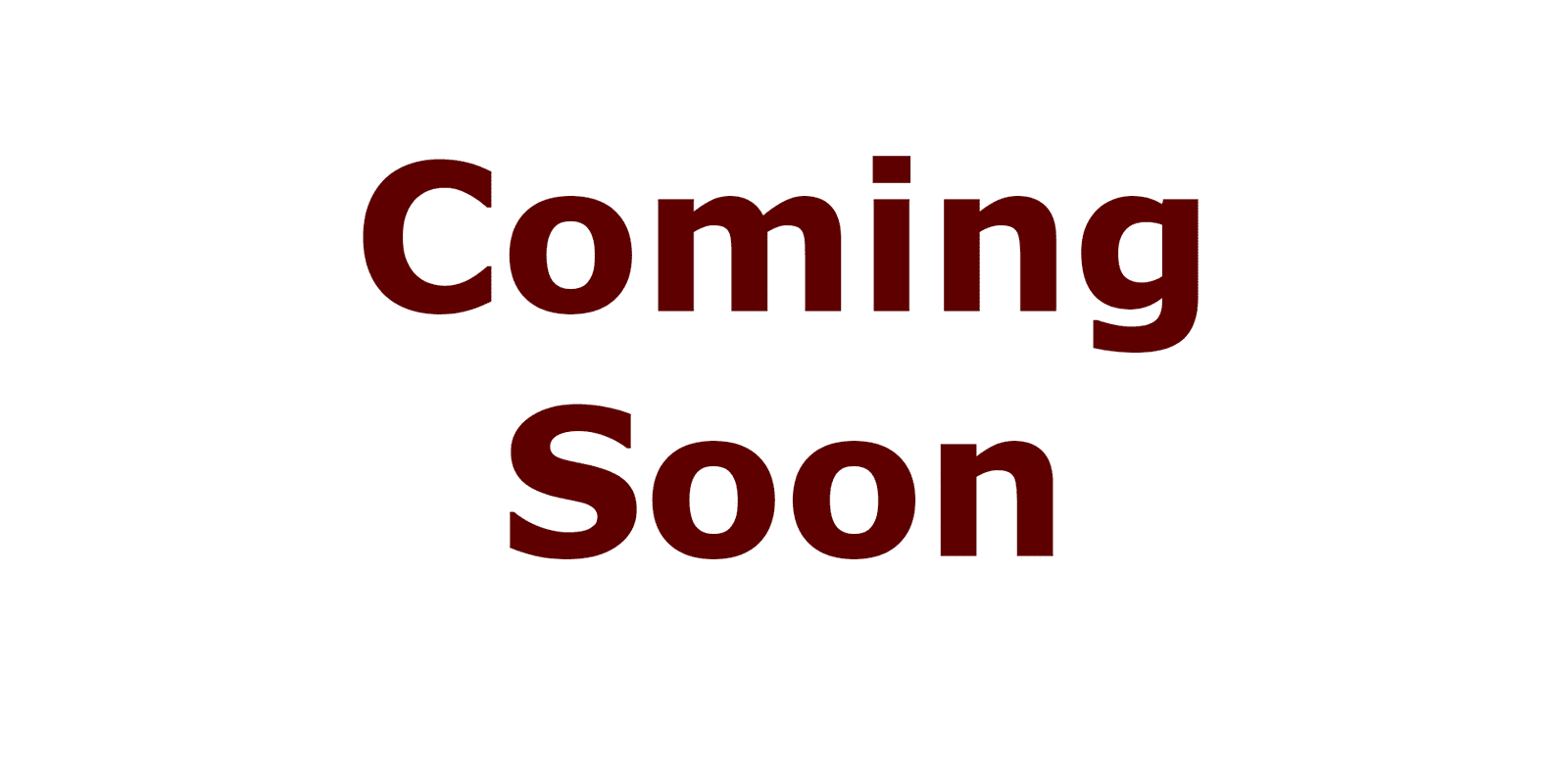
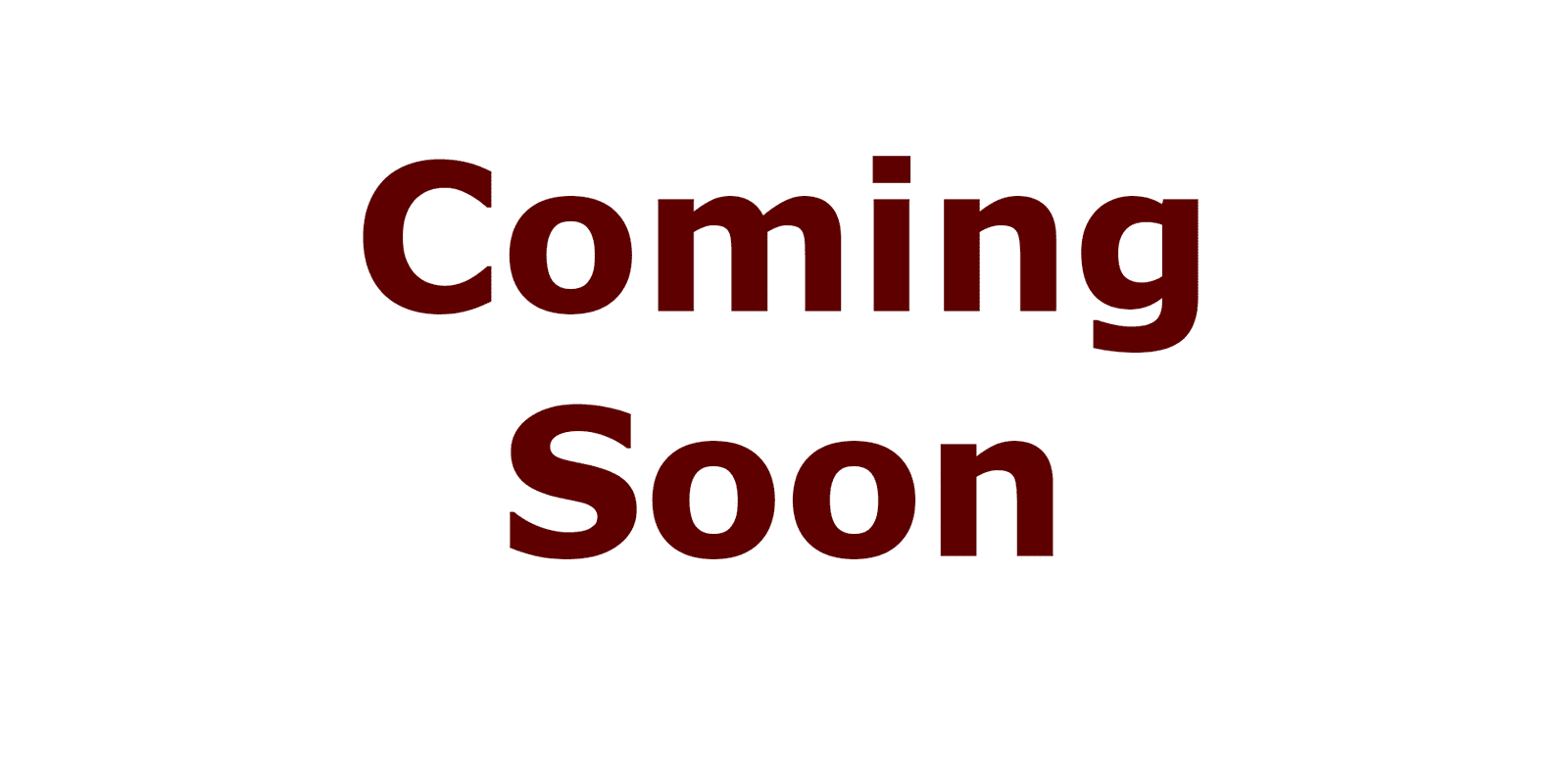
Short Shot
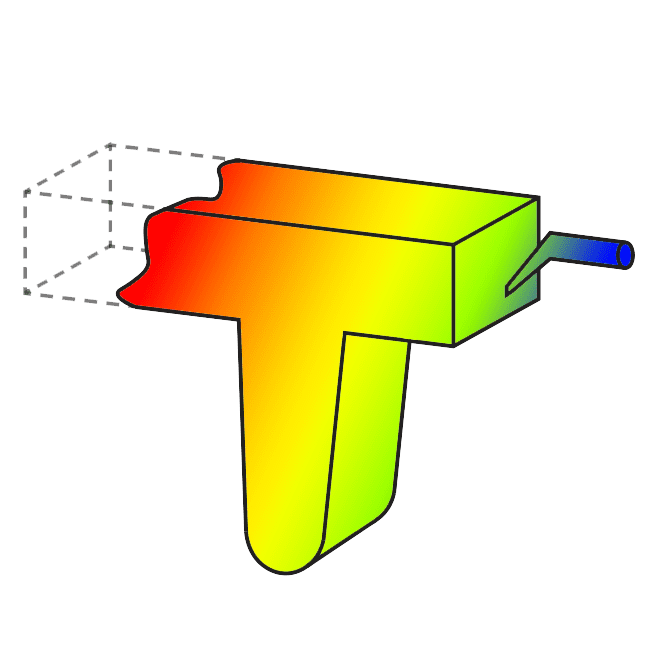
This problem often occurs at the start of the production of a new parts. The cavity or cavities may not be filled. Of course, if the material does not fill the whole mold, the part obtained will be incomplete in addition to having really bad properties. Normally this is due to the flow of plastic solidifying at the front due to temperature.
Here are some causes:
- The polymer too viscous ;
- Flow length too large ;
- Insufficient compacting pressure (holding pressure) ;
- The injection volume (shot size) too low ;
- Inadequate air release when filling.
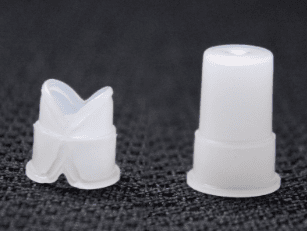
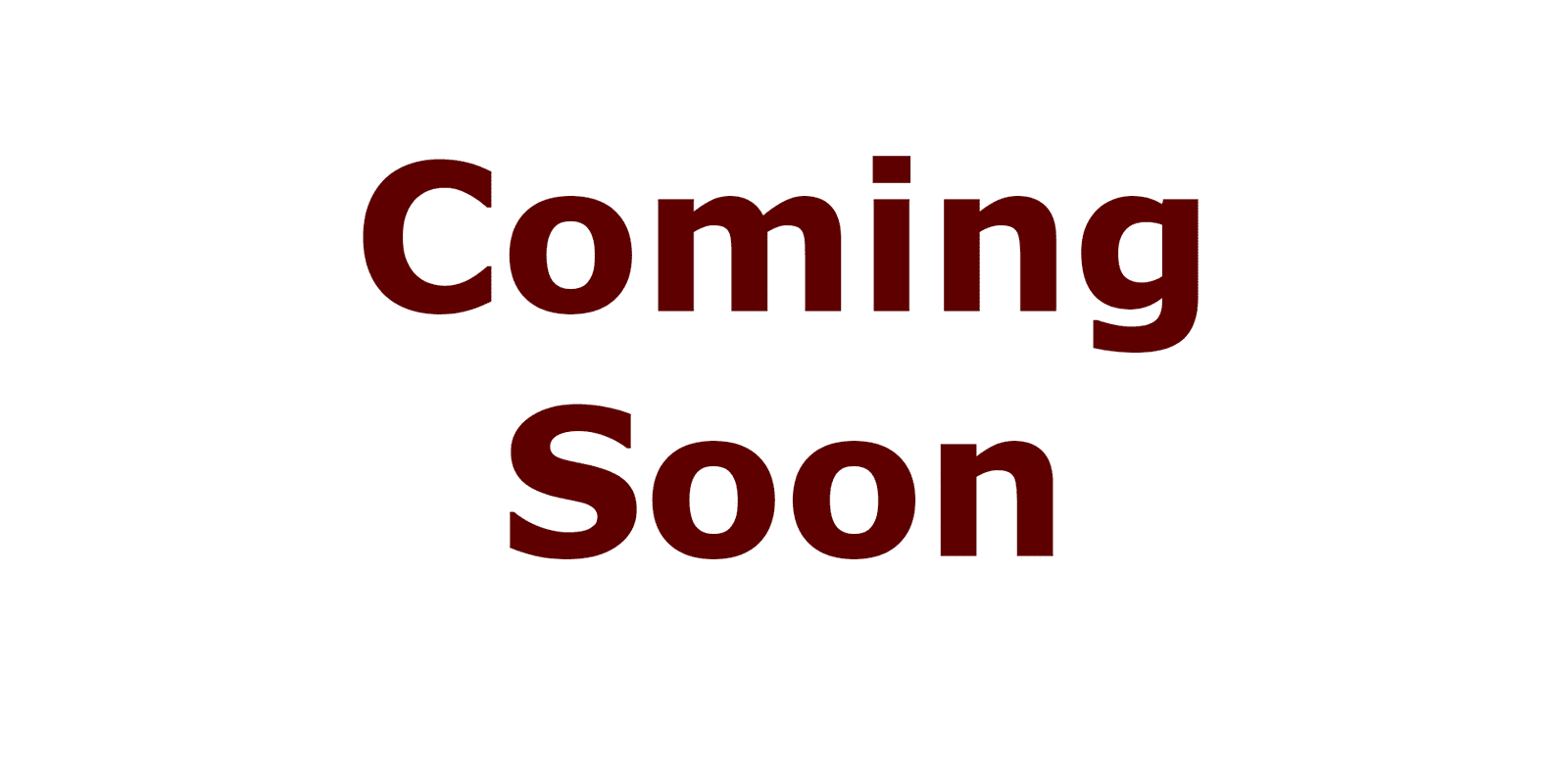
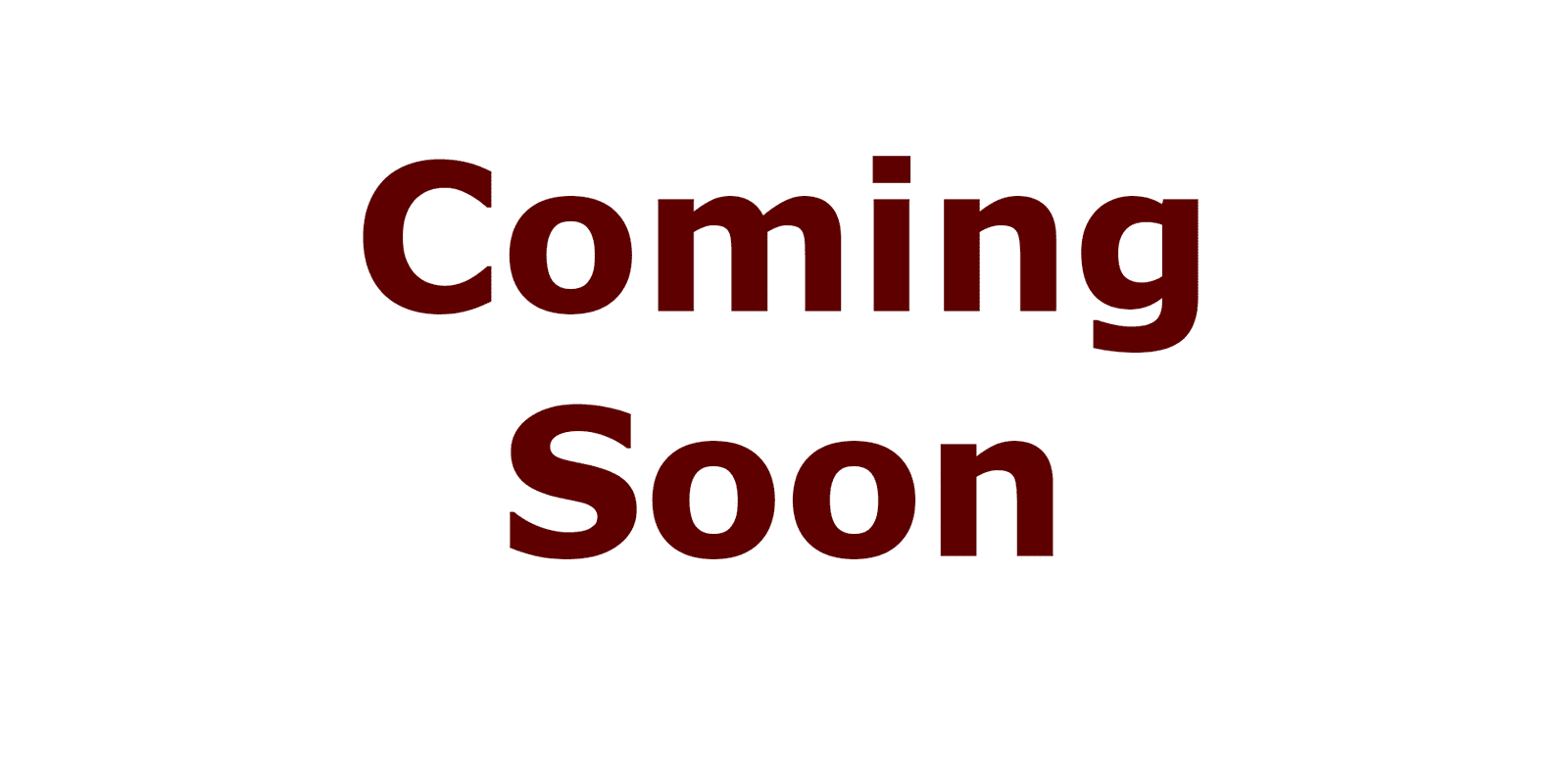
Sink Marks
Sink marks are depressions formed on the surface of a molded part. Although very small, they are often quite visible, given the way they reflect light. The visibility of sink marks depends not only on their depth but also on the color of the part and the texture of its surface.
Here are some causes:
- Significant variations in thickness at the molded part ;
- The injection threshold is not located in the thickest region ;
- Compaction pressure is insufficient ;
- An insufficient compaction time ;
- An insufficient shear rate at the polymer level.
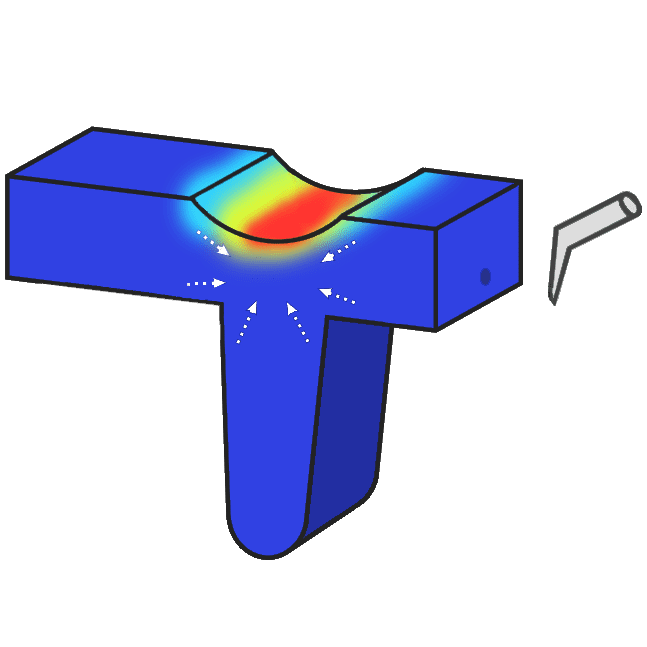
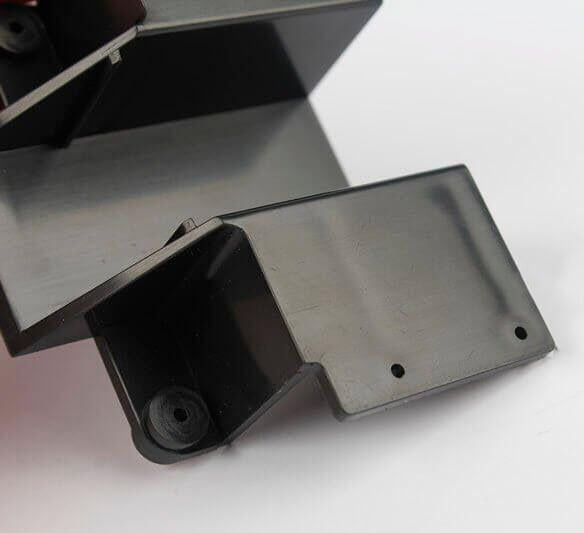
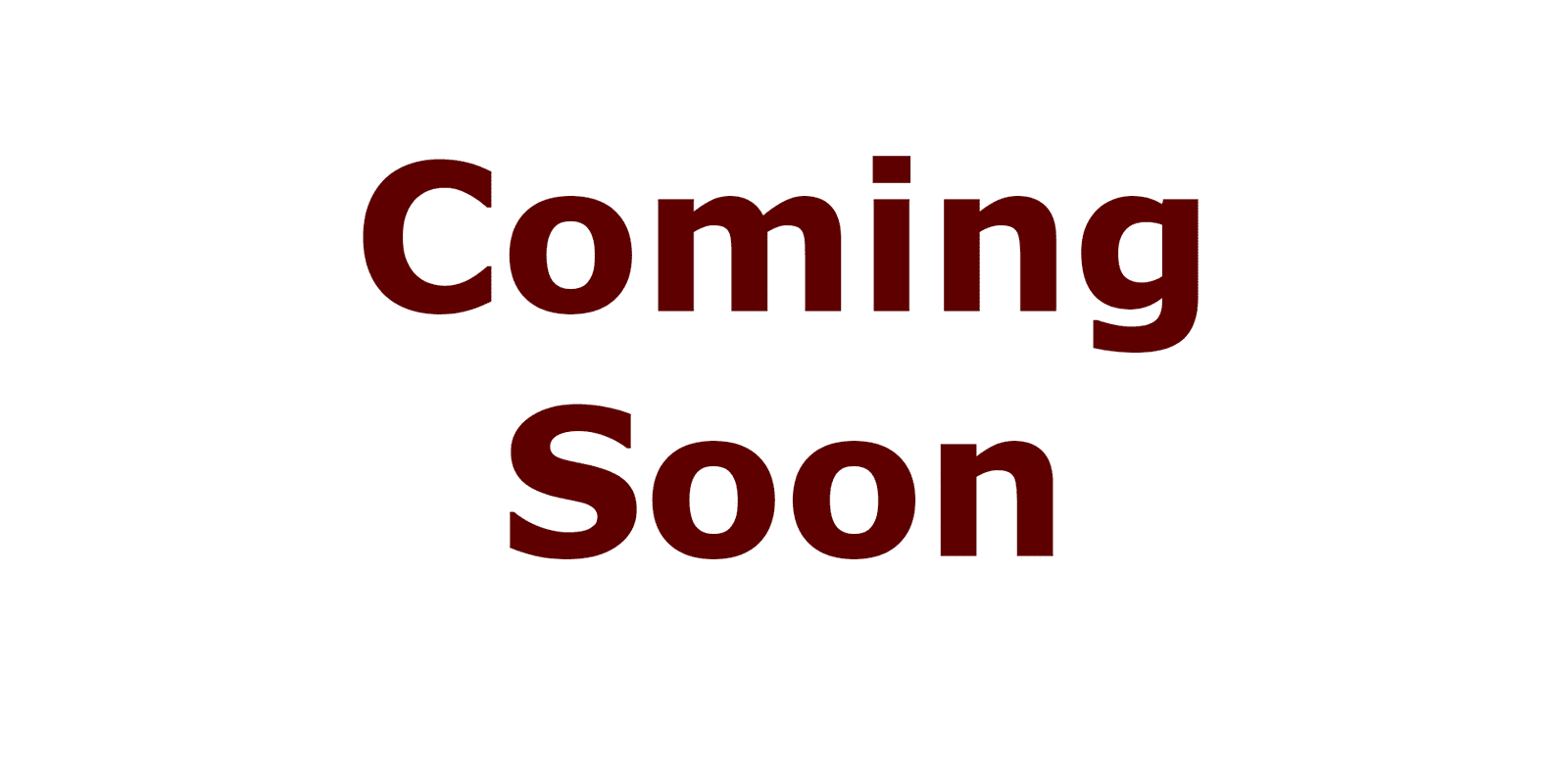
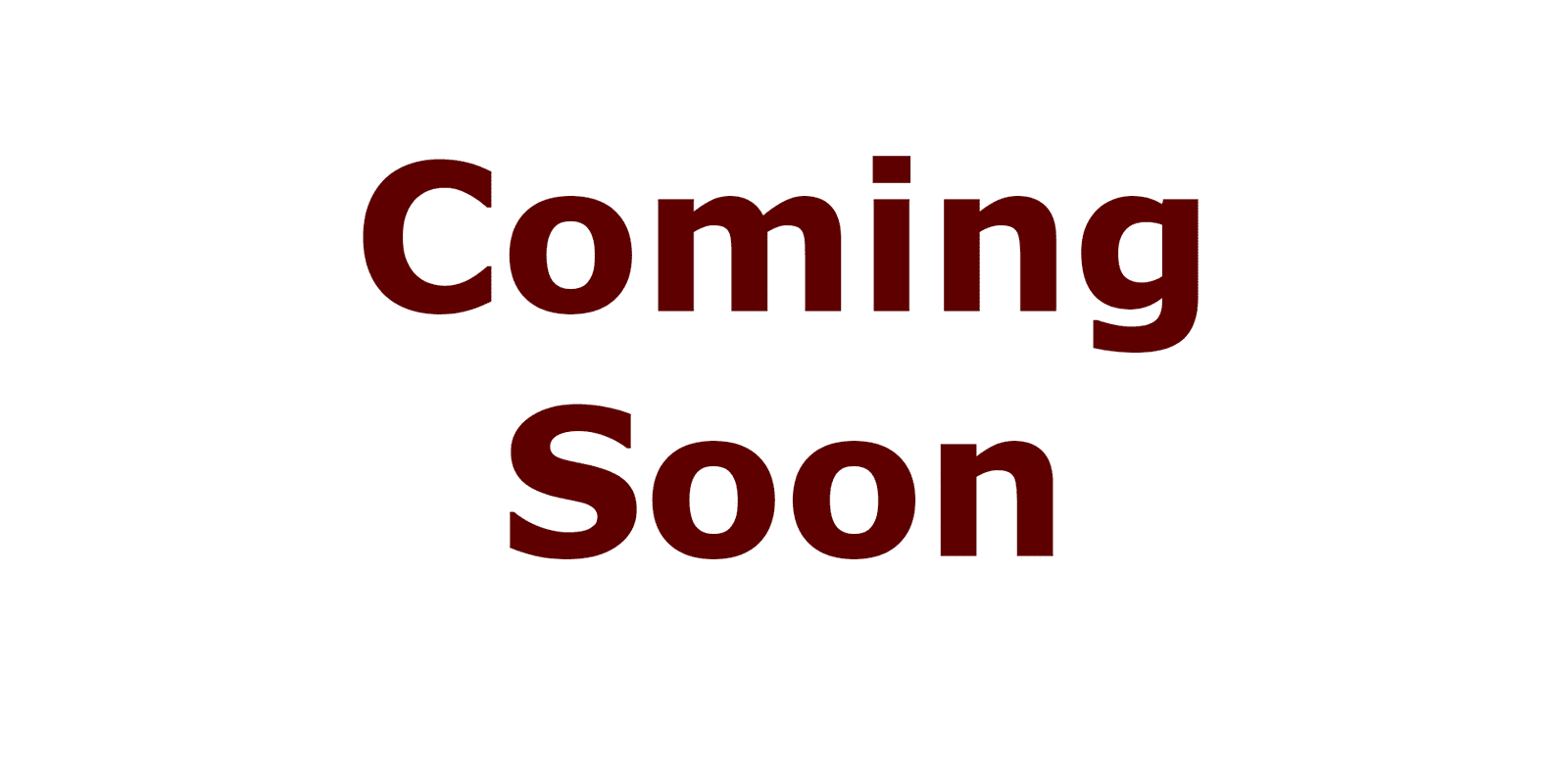
Splay
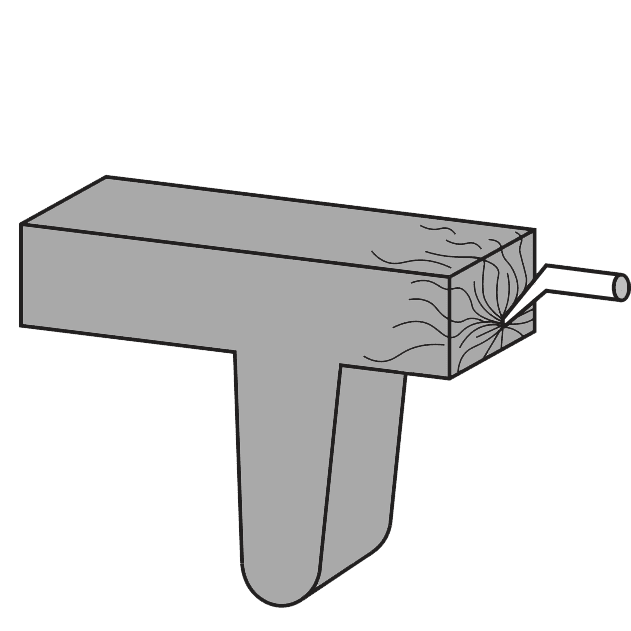
The splay marks are a visual problem observable on the surface of the casting. They can set themselves to a blemish that looks like scratch marks. These marks are created by tiny gas bubbles that move across the surface of the part during the injection.
Here are some causes:
- Presence of humidity in the polymer or in the hopper ;
- Degradation of the polymer or its additives ;
- Decompression after the dosing is too high.
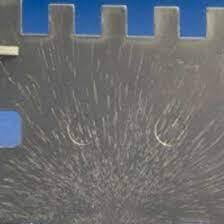
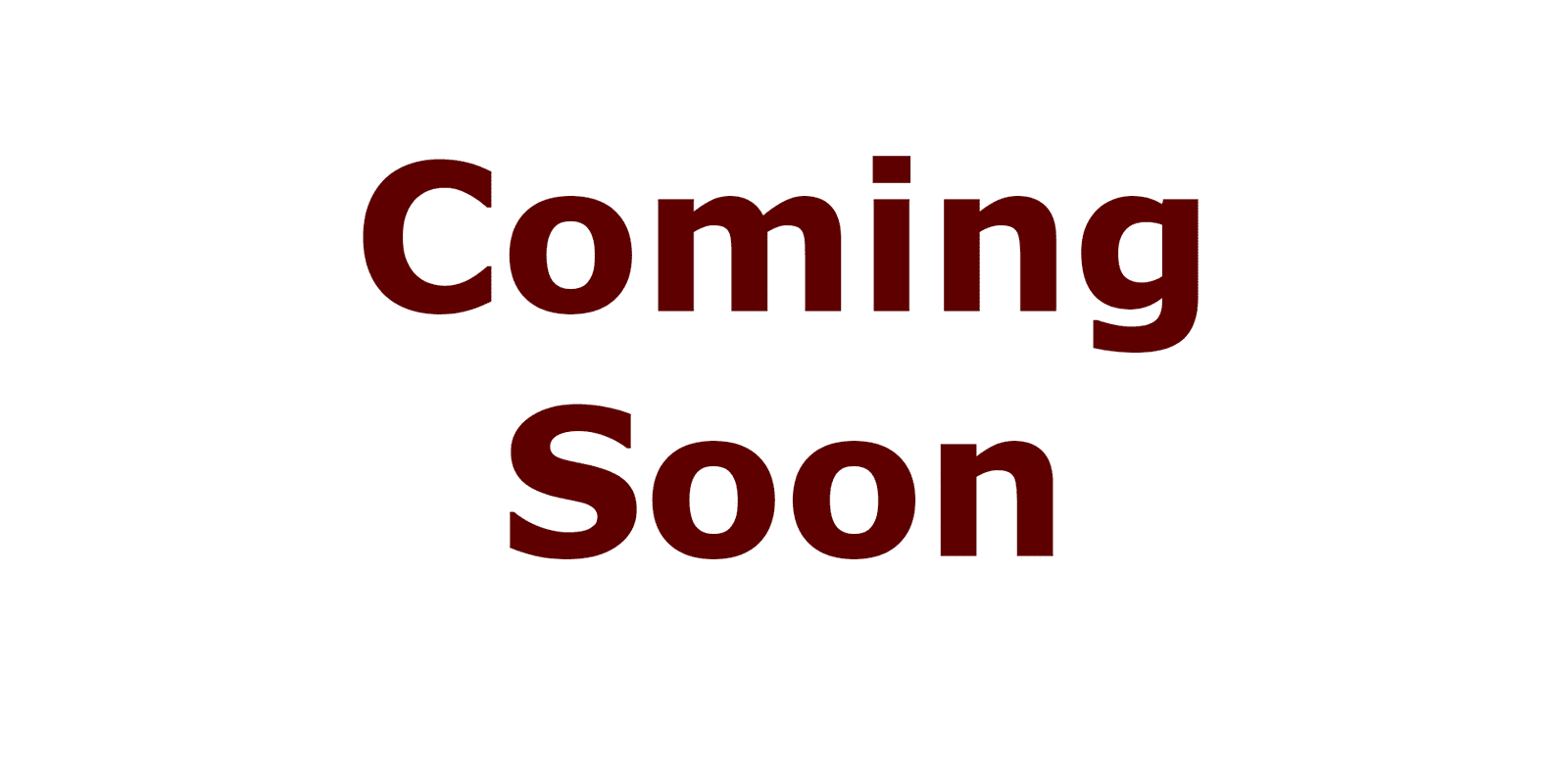
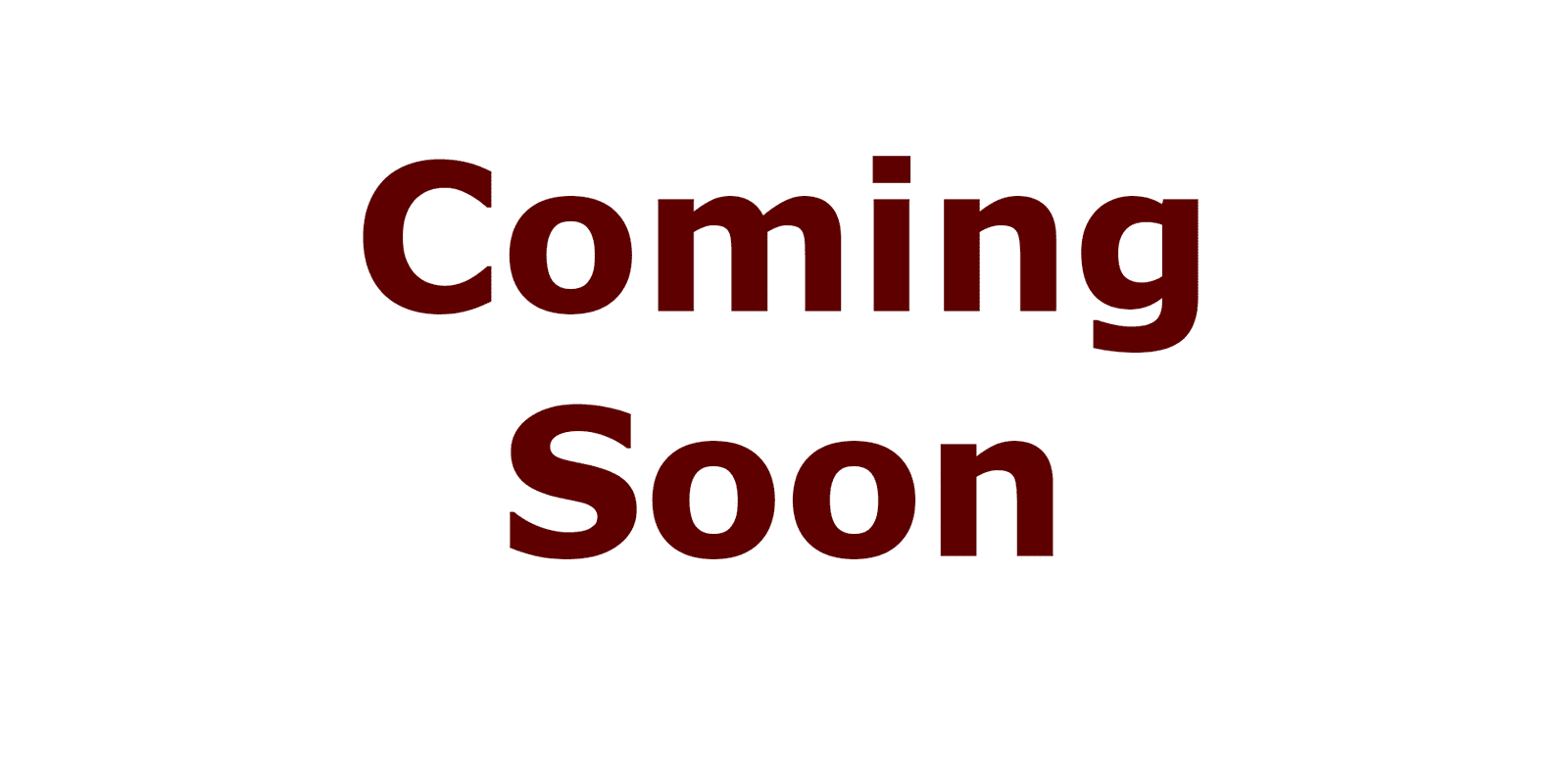
Voids
Voids are holes that form inside a part. They arise when the exterior coating of the part is sufficiently firm to resist shrinkage forces and thus prevent the appearance of shrinkage. Voids can cause serious problems with the structural performance of the part or even aesthetic problems in the case of transparent parts.
Here are some causes:
- Significant variations in thickness at the molded part ;
- The injection threshold is not located in the thickest region ;
- Compaction pressure is insufficient ;
- An insufficient compaction time ;
- An insufficient shear rate at the polymer level.
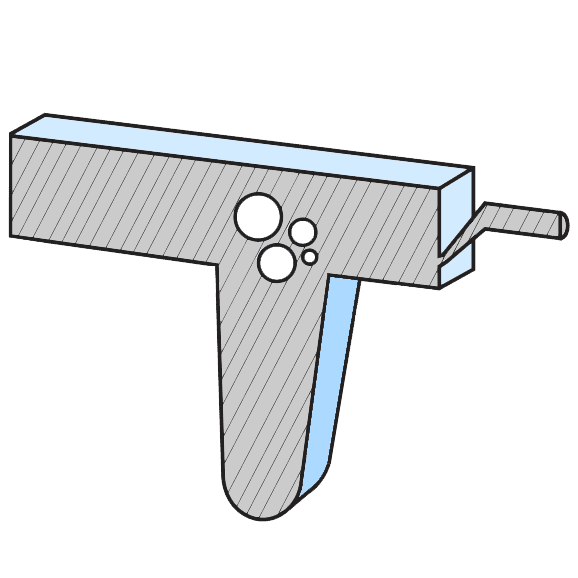
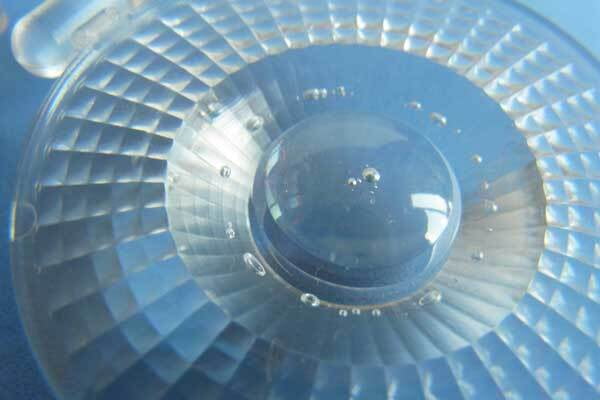
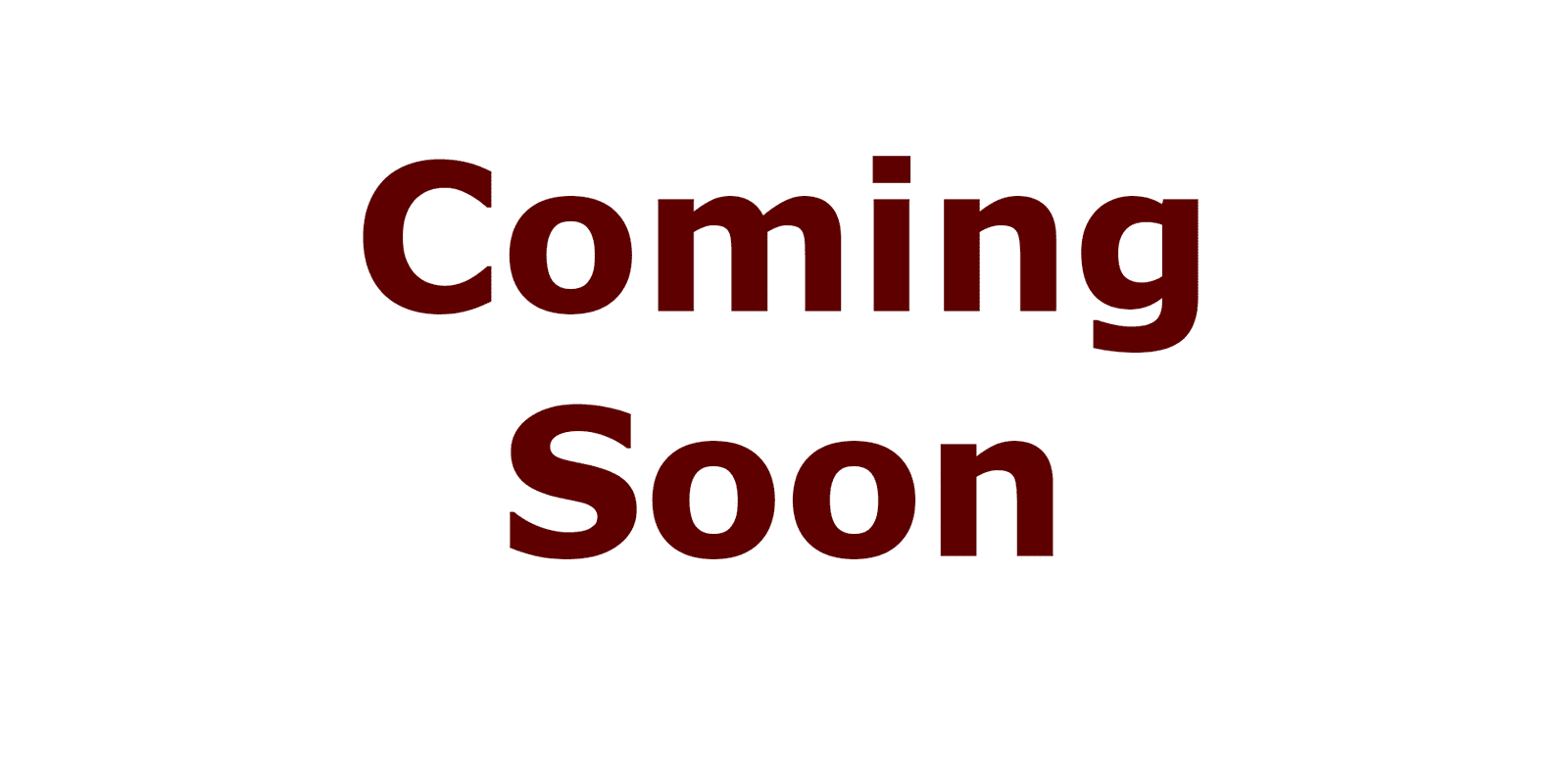
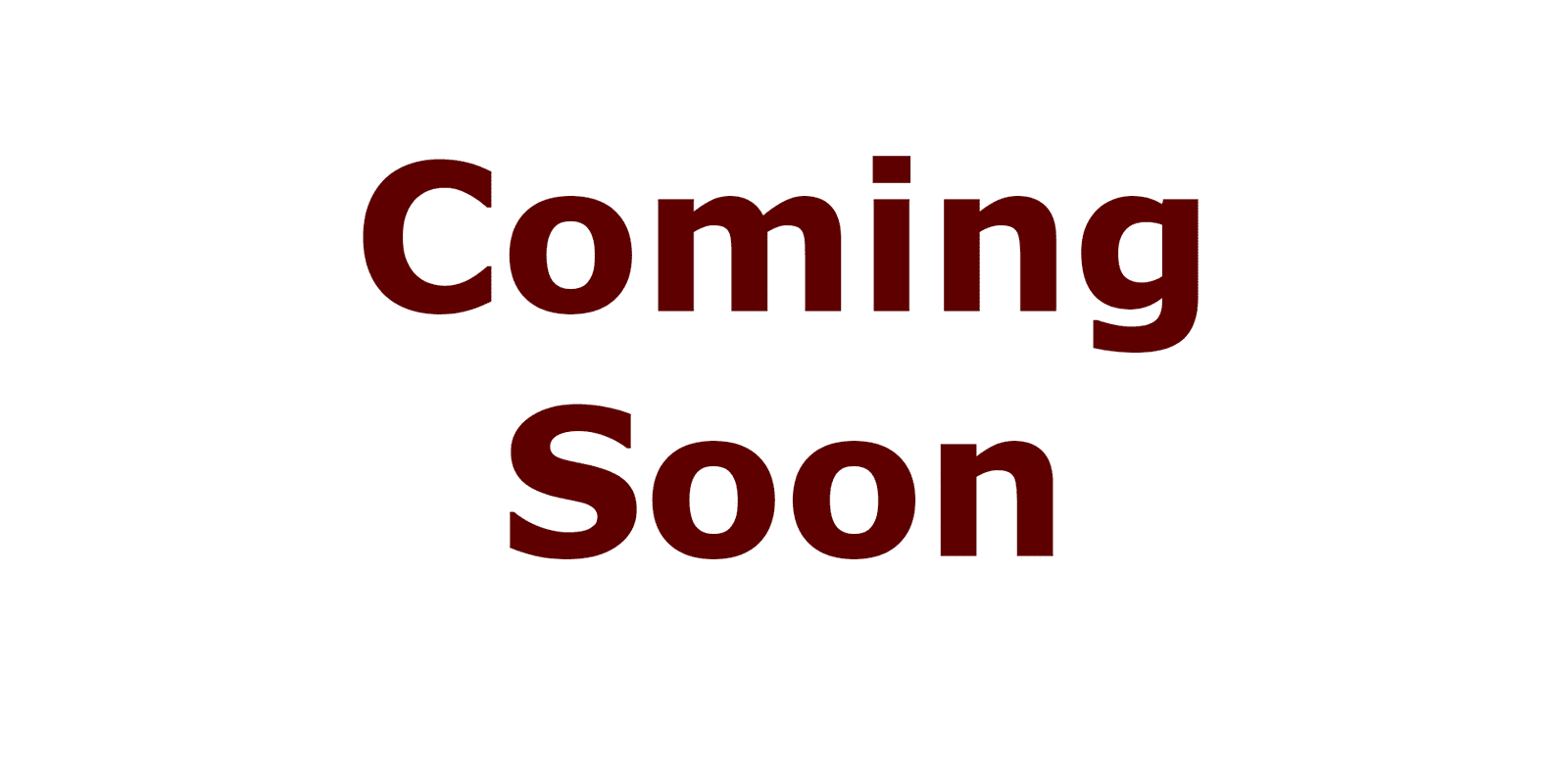
Warpage
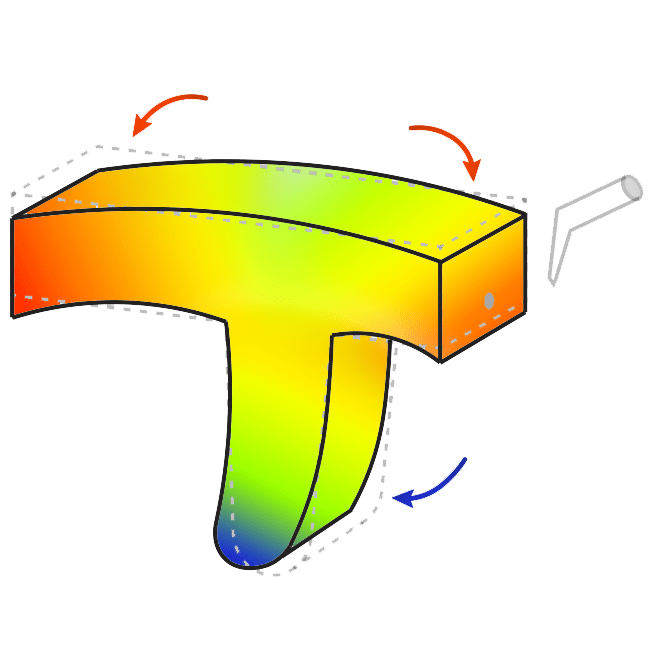
Warping is the problem with the most causes. Almost all values are caused by the warp of a coin. Among other things, Warping takes place when the internal stresses vary in the material as a result of a variation in shrinkage. Parts exhibiting warpage may not work in assembly or may be aesthetically unacceptable.
Here are some causes:
- Non-uniform room wall thickness ;
- Thick sections shrink more and cause warping ;
- The compacting pressure is too low ;
- The compating time is too low ;
- The integration of fiber into plastic.
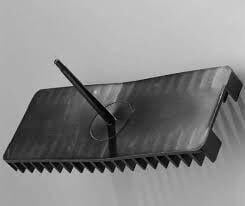
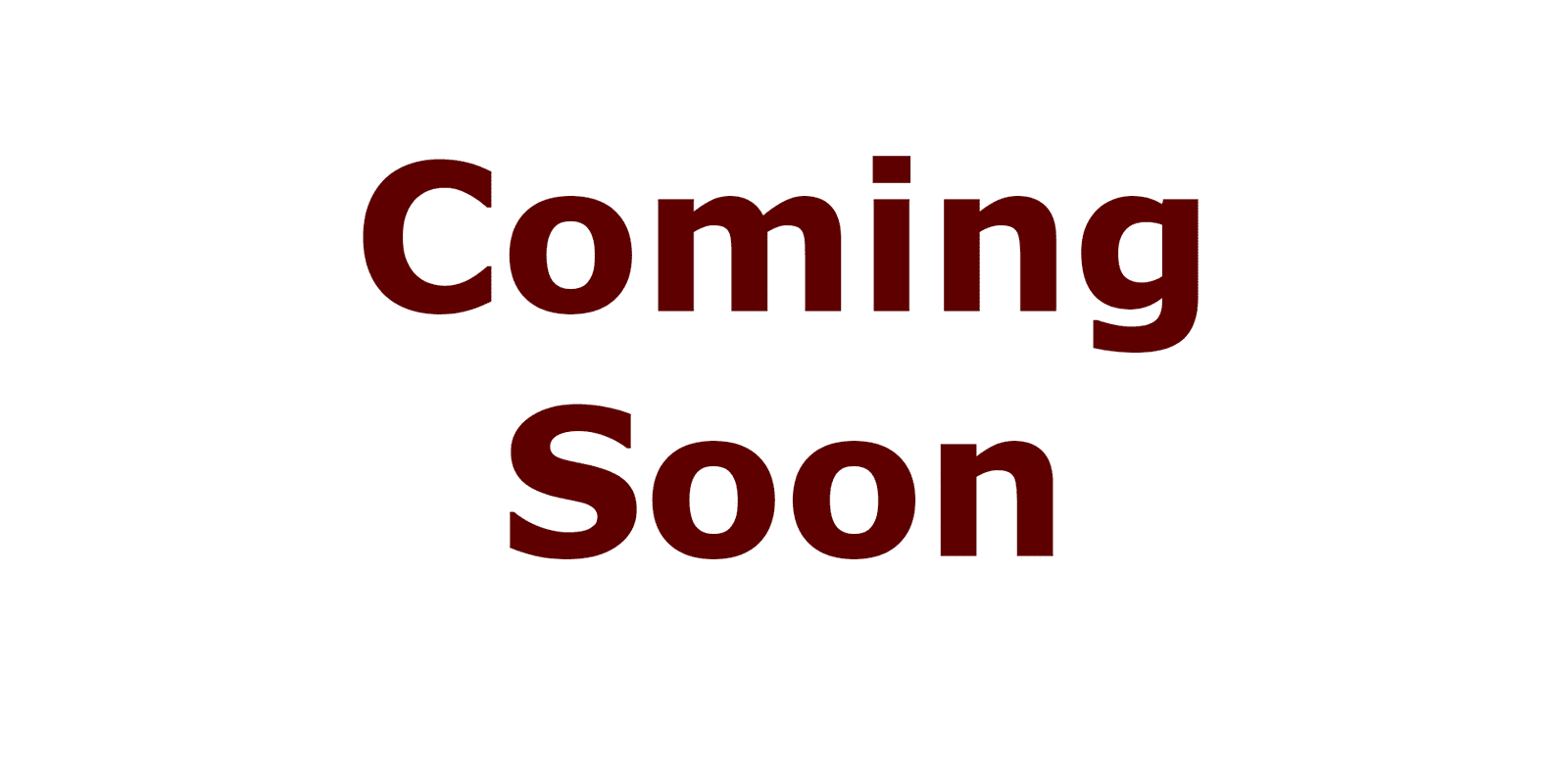
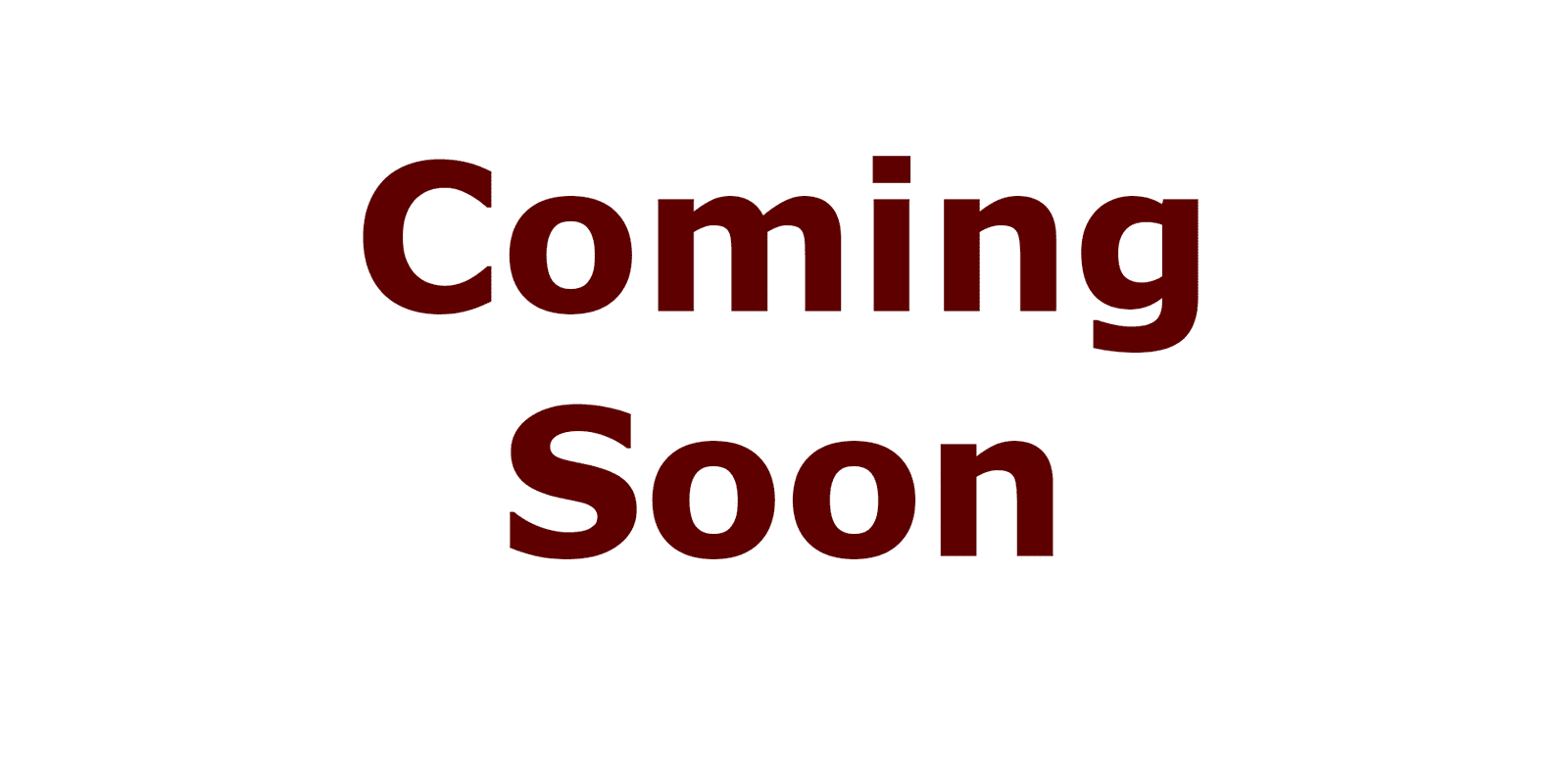
Weld Lines
A weld or melt line that forms on a plastic part can cause structural problems and/or be unacceptable in appearance. They can be caused by holes or inserts in the part, multiple gates or varying wall thickness, where hesitation or race field effects occur. If the two flow fronts cool before the meeting, their fusion is not optimal and can cause a defect in the part. This defect can easily appear on the piece.
Here are some causes:
- Filling too slow ;
- Feed system imbalance (family mould) ;
- Improper mold temperature ;
- Incorrect material temperature ;
- Defective air exhaust system.
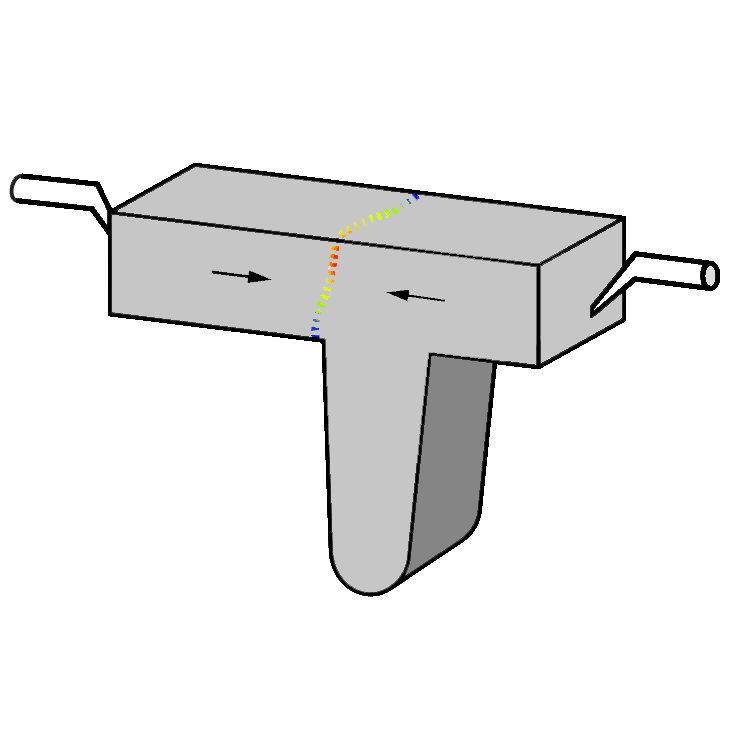
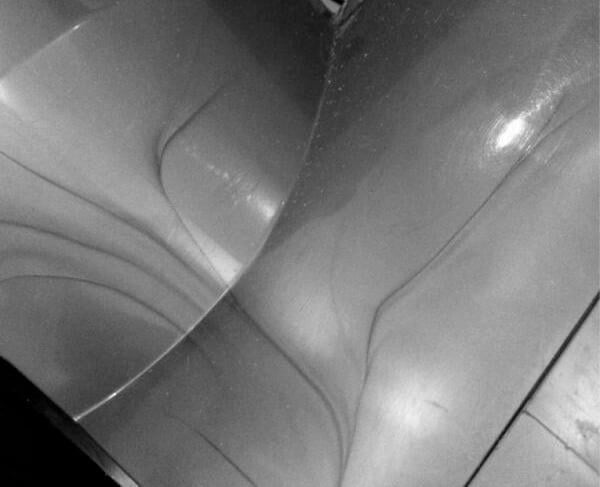
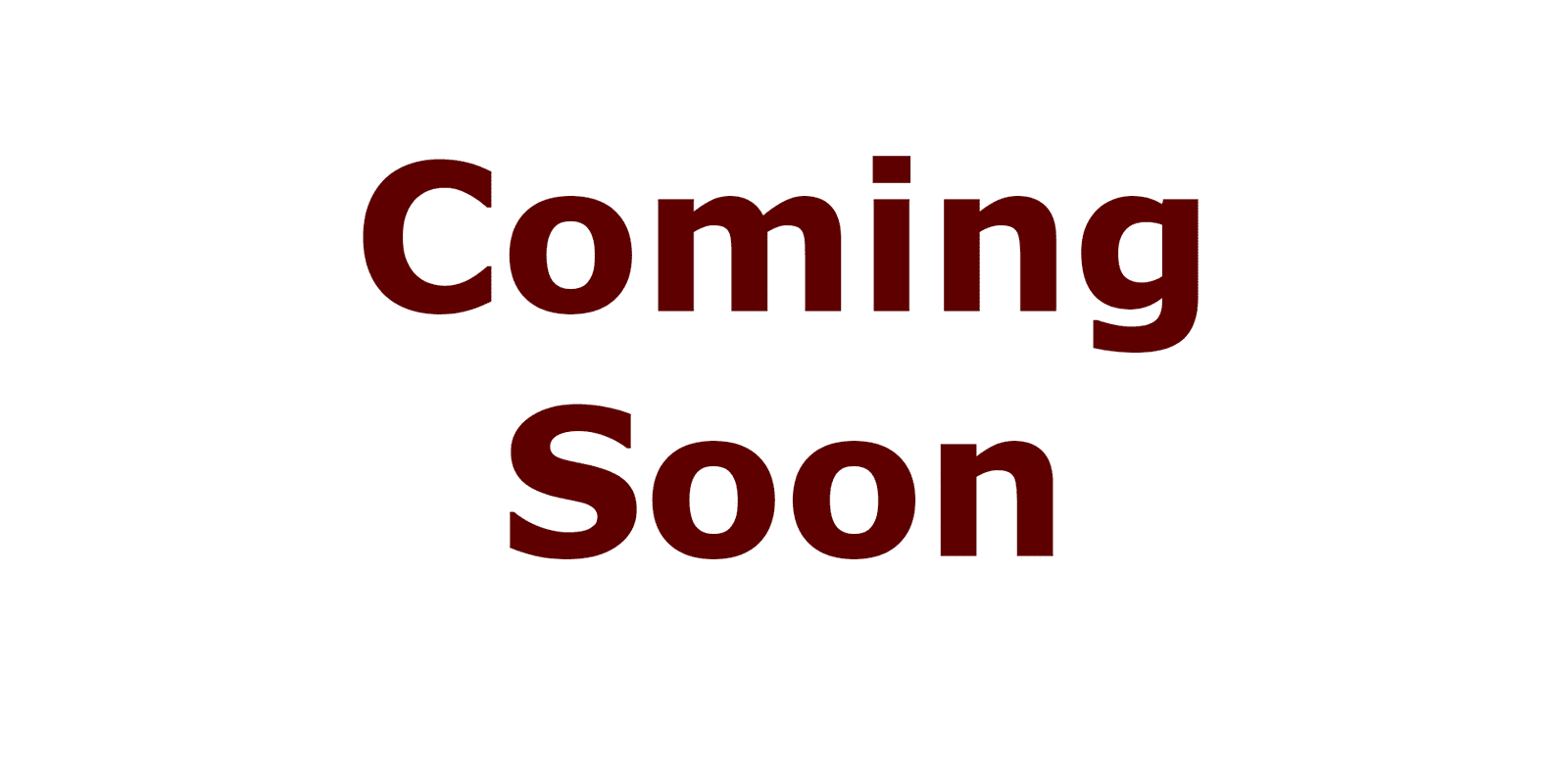
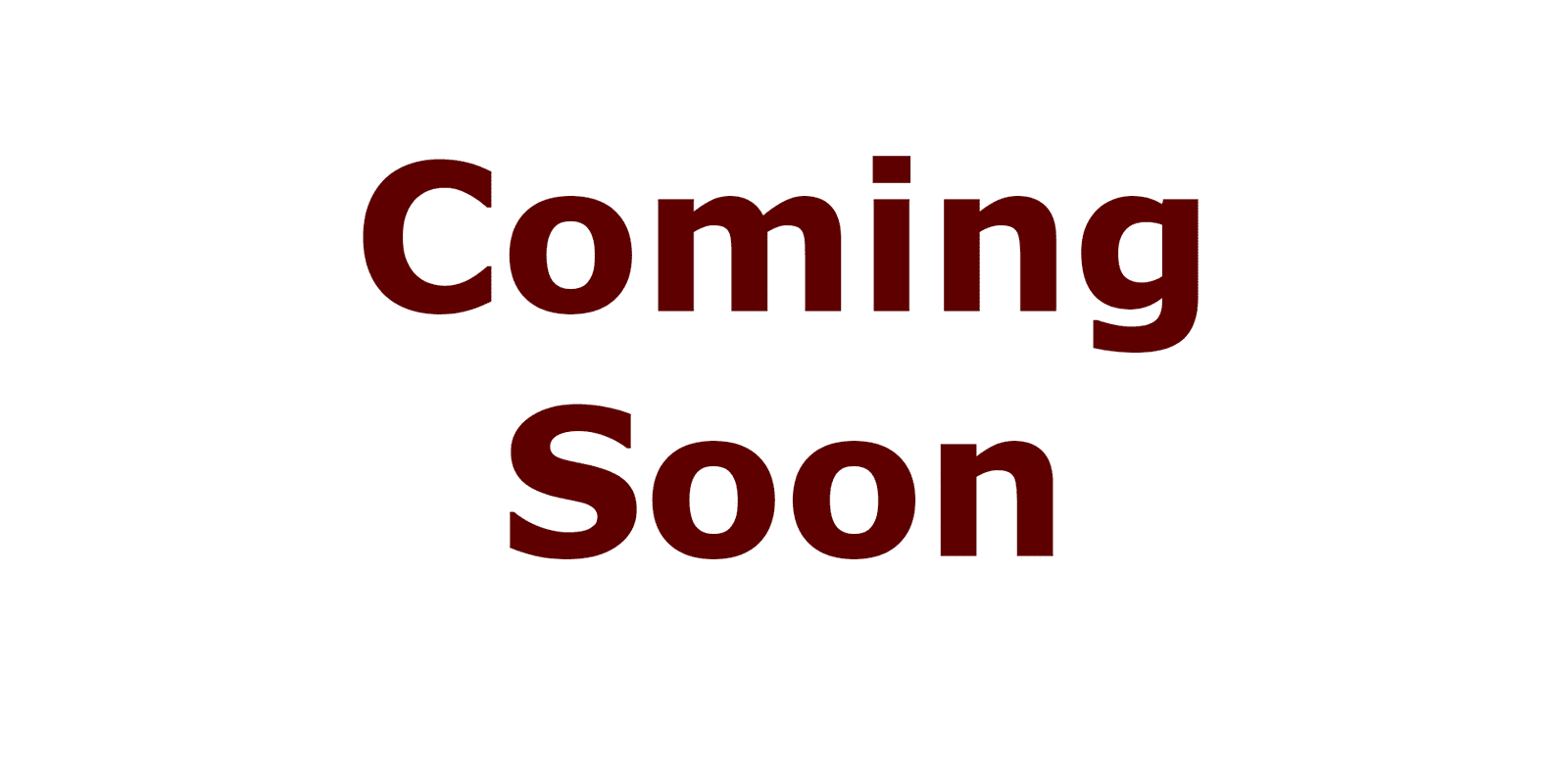